1、适时制生产方式的发展和核心理念
作为世界最富盛名的汽车制造业之一,丰田公司创立的独具特色的适时制生产方式被业内人士津津乐道。丰田公司极力推行适时制生产方式,这种方式表现出了巨大的优越性,有效控制了成本。现在这种生产方式顺应了时代的发展和市场的变化,它虽发展于丰田公司,但又不仅仅适用于汽车制造业。运用这种方式节约了相关人员费用、仓储保管费用,降低生产成本,提高企业的盈利水平。
作为一种彻底追求生产过程合理性、高效性和灵活性的生产管理技术,适时制生产已被运用于众多企业中。
它的基本思想是:只在需要的时候按需要的量生产所需的产品。
适时制生产方式的核心是:消除一切无效的劳动和浪费,在市场竞争中永无止境的追求尽善尽美。
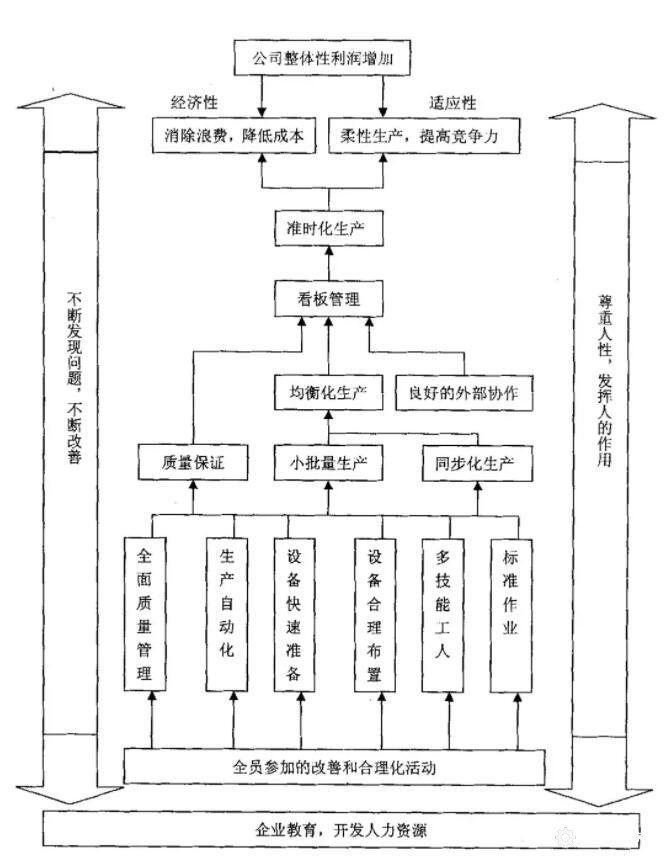
适时制生产方式的技术体系
2、适时制在丰田公司的应用情况
适时制生产方式一直是日本丰田公司核心竞争力与高效率的来源。自从能源危机引进此种生产方式,丰田公司跻身于世界汽车制造业的领先地位。公司为充分发挥适时制的作用特意创造了两个条件,
第一点是使零部件供应商及其装配厂尽可能靠近销售市场,这样直接降低了产品的运输成本,也减少了因库存时间太长而浪费了存储成本。
第二点是产品规格变化小。他们一面提高汽车标准件程度,一面宣传这样做所要付出的额外成本。
这样不仅提高了汽车销售价格但却又不会增加零部件在生产上的复杂性,有利于采用适时制的生产流水线。
丰田公司采用适时制方式从中受益良多。它提高了库存的周转次数,尽量避免等待装配的时间的浪费。
据丰田公司统计,该厂某部件全年需要量为9000件,自从库存周转率提高到原来的三倍之后,最高库存量减少为3000件,并且这3000件又能够快速投入使用,可见适时制带来的好处十分明显。
另一方面,适时制减少了装配用的零部件库存量,从而减少了库存占用的流动资金和仓库空间,这样做有效避免了货物因贬值带来的额外风险。
丰田公司曾这样描述适时制带给他们的好处:流水线可以为客户的单独制定的汽车进行生产,而客户等候的时间小于1天(平均3汽车的装配时间为8分钟)。
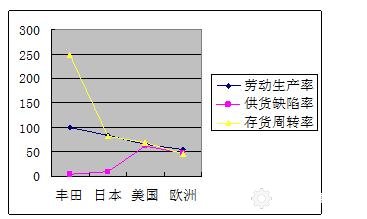
丰田公司和其他地区平均指标比较
3、均衡化生产与设备装换调整
均衡化生产是适时制生产方式的重要基础。在汽车的生产过程中,后道工序在必要时可从前道工序领取必要数量的零部件,但这种方式若经常没有规律的变动势必会捣乱工序的正常顺序,从而造成人力物力的闲置跟浪费。为避免这种情况发生,丰田进行了均衡化生产。
不仅要求数量的均衡化,还要求质量的均衡化,即总装配线向各前工序领取零部件时要均衡取得零部件,实现混流生产。
丰田公司设置均衡化生产时努力让装配线上的生产变动最小,防止在某段时间内集中领取同一种零部件造成前方工序的闲忙不均而发生混乱。
换句话说,丰田的均衡化使得零部件被领取时的数量变化达到最小,这样做的好处就是各工序以一定的速度和数量进行生产,免得引起生产混乱。
丰田不仅把均衡化生产运用在生产线上,更使其成为适应市场需求变化的重要手段之一。
通过均衡化生产,各个生产线每天同时生产多种型号的配件,这种小批量、多品种的混流方式具有很大的弹性,能够迅速地适应市场需求的变化。为了实现均衡化生产,有一点非常困难,那就是设备的快速装换调整。
丰田公司各个工序采取多品种、小批量的生产方式,需要频繁地从前道工序领取零部件,这种生产方式注定丰田不能大批量、连续地生产单一零部件。为了实现设备的快速装换调整,丰田公司的生产现场人员经过多次实验与不断努力,成功地将所有大中型设备的装换调整操作都控制在10分钟以内完成。
丰田公司的要领就是把所有作业划分为两大类:外部装换调整作业和内部装换调整作业。外部装换调整作业就是指能够在设备转运之中进行的装换调整作业,而内部装换调整作业指那些必须或只能够在设备停止运转时才能进行的装换调整作业。
丰田公司要尽量把内部转变成外部,缩短作业时间,从而保证迅速完成装换调整作业。所以丰田应当把设备的快速装换调整视为提高企业竞争力的关键因素之一。
4、全面质量管理
适时制的另一个重要技术支撑是以确保零部件和制品的质量为目标的全面质量管理,把质量作为生存之本是企业的共识。
丰田公司的适时制生产方式有效制止了过量生产,从而把生产系统中的零部件在生产储备量降到几乎为零的程度。这迫使生产系统中每道加工工序的作业人员必须生产出100%合格的零部件,否则一旦出现不合格产品会破坏正常的适时制生产。
丰田公司的适时制生产方式需要逐步减少生产系统中的零部件在产品储备,要对生产现场进行改善,提高零部件的质量。
丰田公司奉行的“适时制生产方式加全面质量管理”使得生产系统的功能日趋成熟与完善,它令零部件的产品储备量减少,前后工序的衔接更加紧密。这,种以“减少库存、发现问题、改善现场、提高质量、降低成本”为周期不断循环是丰田公司的内在机制,是控制成本的有效手段。
5、合理化建议与良好协作关系
丰田公司在内部管理中坚决采用合理化建议制度,激发员工的创造性思维以提高公司业务水平。
光只有建议并不足够,良好的协作关系在现如今专业化分工高度发达的今天对控制成本有着非常重要的作用。首先,丰田公司的库存费用就大大降低了。其次,丰田公司的产品生产周期大幅度缩短了。
6、召回事件反映的问题及反思
丰田在2009年年末却突遇召回事件。从2009年11月26日到2010年2月9日,丰田公司先后因“脚垫门”和“踏板门”“刹车门”在全球召回800万辆车子。
究竟是什么原因导致丰田公司未能充分发挥适时制的优势而有此恶劣事件?其中一个原因就是丰田过分强调战略扩张和成本削减,影响了内部控制执行效果。
过去几年丰田迅速空大生产规模,大量在海外建厂。这种高速扩张战略使得其不得不大量招聘低成本的工人,并且为了尽快收回投资成本,丰田无暇为工人提供适当的训练从而让他们适应适时制生产方式对人员技能的要求。没有恰当的培训,人员素质不可避免的下降,为召回事件埋下了伏笔。
同时面对快速扩张造成的成本压力,公司选择对产品进行“瘦身”,为压缩成本跟争取时间,产品设计前期的开发和试验也被简化甚至忽略么,最终酿成杯具。
丰田公司的召回事件引人深思,在积极运用适时制生产方式下要同时做好内控工作,不能为了节约成本而省掉了很多必须的步骤。丰田初衷是为了减少成本取得更多利润,但却因为召回事件不得不付出更多的费用。
7、尾巴
企业要改善经营机制,提高经济效益,加强经济核算必须加强成本控制,只有把成本控制好了,才能提高企业的实力,使企业在竞争中立于不败之地。
丰田公司运用适时制生产方式有效对成本进行控制,并保证了产品的质量。这种方式需要从经营意识、生产方式到管理方法不断更新,与时俱进才能保障它的高效性。而召回事件同时也给丰田公司敲响了警钟,不能过分关注降低成本而忽略了产品的质量问题,要根据自身情况制定适当的扩张战略。