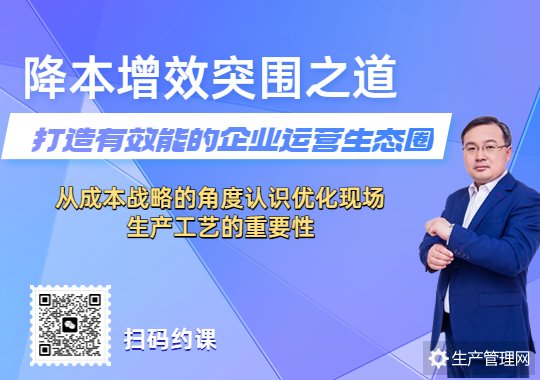
降本增效突围之道
——打造有效能的企业运营生态圈
课程背景:
2020年突如其来的疫情给世界的经济形势带来了新的挑战,中国企业的未来将何去何从?给我们带来了更多的变数。危机当中也蕴含着机遇,中国工业优势在于市场广阔和新型人力资源的开发,特别是“一带一路”政策实施,中国的工业时代将进入一个新纪元。
中国的工业劣势也很明显:大中型国有企业创新转换能力差;民营企业运营质量不稳定,工业发展后劲不足, 企业将面临着有史以来最大的挑战,工厂大量制造的低成本竞争的年代已经一去不复返了,未来的管理突破口在于生产效率的提升及成本管理和质量的控制。
动车比传统的火车跑的快三倍,主要原因是动车的每节车厢都有一个发动机,而传统的火车只有前面车头的牵引后面的推动,引申到管理理念就是“火车跑的快全凭车头带”这种理念显然是过时的口号,现代正确的理念是“发挥每节车厢的动力,全公司动起来”。
实践证明我们完全可以实现轻资产运营和差异化运营,使企业的利润持续增长。这个运营战略的支撑有赖于生产人. 机. 料. 法. 环的合理匹配和内部生态链管理提升的推行。让我们专业和实战的导师和大家一起分析和学习吧!
课程收益:
■ 在新常态经济形势下,企业从内部管理如何的转变;
■ 从信息流和实物流的角度来分析“企业烧钱”的运营模式;
■ 从供应链的角度拓展成本管理与控制;
■ 熟练掌握生产现场常用的解决和改善管理问题的工具;
■ 从成本战略的角度认识工作质量的重要性;
■ 从成本战略的角度认识设备管理的重要性;
■ 从成本战略的角度认识优化现场生产工艺的重要性;
■ 用能理解. 记得住. 用的上的方式,熟练掌握精益生产和质量控制的复杂理论。
课程时间:2天,6小时/天
课程对象:制造业中. 高层管理人员
课程方式:知识讲授+案例+解析+视频分享
课程运用表格及工具:
1. 财务四张报表
2. 价值流程图
3. 采购价格对比表
4. ABC分析法
5. FMEA设计失效模式表
6. 作业过程模式表
7. 作业分解表
8. 丰田生产操作标准七步法
9. ERP系统采购程序图
10. ERP系统仓储程序图
11. MES系统的模拟排产图
12. 日本丰田问题分析八步法
课程大纲
第一讲:我们处在变革的时代
一、历史迫使我们转变
1. 未来企业发展趋势
2. 中、德、日、美工业管理特点
3. 中国企业的困难点及转折点
第二讲:制造业运营价值链分析
一、现代化运营管理模式
1. 精益运营思想在价值链分析中的作用
2. 运营管理由效率转换成效能
3. 运营管理由管理转变成经营
视频:目视化精益工厂理想状态
二、研发、技术、工艺价值链分析及对生产系统的影响
1. 研发与生产成本之间的关系
2. 技术成本与生产成本的关系
3. 工艺严谨性对生产效率和质量之间的逻辑关系
4. 智能化时代研发. 技术新突破点
案例:国内三个大型企业的技术FEMA展示
三、营销价值链分析
1. 创新模式市场营销(案例)
2. 品牌模式营销(案例)
3. 垄断模式营销(案例)
4. 差异化营销管理(案例)
5. 全员营销理念的前身和后世
四、从运营角度看财务价值链分析
1. 正确解读资产负债表
2. 正确解读现金流量表
3. 正确解读利润表
4. 资金流转速度和投入量对运营的影响
案例:一个财务人员顶千军万马
案例:某大型企业财务报表解读
第三讲:制造业内部供应链价值流分析
一、内部供应链价值分析
1. 管理好“入口——采购与原料仓储
2. 调整好“胃口”——生产内部供应链
3. 管理好“出口”——成品库与客户供应链
互动:人的身体与内部运营各部门的关系
二、价值流程分析(VSM)
1. 价值流程分析的原理
2. 价值流程分析的结论
3. 信息流与实物流的误解
1)信息流的浪费才是最大的浪费
2)整理信息流与实物流
案例:一个20天交期如何缩短40%
4. 如何做价值流程图
案例:中车集团价值流程分析过程
三. 采购与仓储价值链
1. 采购成本分析图
2. 供应商评价策略与谈判
3. 采购体系搭建
案例:采购管理ERP智能化建设
4. 原材料储存ABC与采购策略调整
5. 标准库存量的计算与考核
6. 仓储部门三不原则
7. 仓储账. 物. 卡之间的关系
8. 成品库治理实战
案例:仓储管理ERP智能化建设
第四部分:制造业生产系统价值流分析
一、改善从识别和消除浪费开始
1. 生产系统七大浪费现象
2. 生产现场浪费如何形成的?
3. 生产现场浪费有什么危害?
4. 生产浪费现象治理的分类
二、精益准时化物流控制搭建
1. 拉动式计划与推动式计划
2. 生产能力均衡化(TOC理论)
3. 生产计划的“前生和后世”
1) 生产计划在整个运营系统的地位与作用
2)生产MES系统推进的组织改善
3)生产调度. 生产物流. 生产管理的关系与分工
案例:MES系统模拟排产
4. 单件流的计划与实施
案例分析:如何做拉动式计划
三、精益生产人、机、料、法、环、信息的管控
1. 日本丰田的自働化蕴含着人的秘密
2. 设备TPM中的OEE是衡量生产效率的最佳指标
3. 物流及时化是保证生产效率的根本
4. 现场6S管理是生产环境治理的最佳方法(全图式讲解)
5. 生产方法的调整策略
1)应对小批量. 多品种的技术——SMED
2)质量保证——标准化建设. TQM
3)人机互动最佳手段—— IE工程学
3)丰田问题改善八步法是生产改善最全的工具
5. 信息流建设
1)智能化工厂的特点
2)纵向集成化的工厂
3)端对端集成工厂
4)横向集成工厂
5)智能工厂的未来发展四大趋势