一、生产来料及仓库问题点
1、来料不良多。2、来料不良信息未及时反馈给供应商。
3、缺乏有效手段促进供应商改善。
4、供应商来料数据未有效统计与可视化。
5、仓库呆料过多。
6、仓库物料查找不易。
7、仓库存在安全隐患。
8、仓库标识不充分。
9、仓库物料系统信息未及时更新。
10、仓库存在脏乱状况。
11、仓库距离生产现场过远。
12、仓库产生过失窃状况。
二、生产计划及采购问题点
13、生产计划信息传递不及时。14、生产计划中的优先顺序存在不合理之处。
15、生产计划不精准。
16、因缺乏与客户及时沟通,经常有插单状况。
17、市场人员不负责任的许诺,导致生产无法跟进。
18、生产未严格按生产计划执行。
19、从销售到采购的信息流动未完全打通,存在信息阻隔。
20、采购人员或销售人员与外部有不当交易。
21、采购人员凭个人喜好给供应商下单,而非根据供应商的实际状况下单。
22、采购人员对供应商生产实际进度缺乏掌控。
23、供应商的样品与实际生产有明显差距,管理人员存在疏于管控的失职。
24、因对供应市场的状况不了解,导致某供应商断供时,无法从其他来源来快速获得供应。
25、供应商管理人员经常去供应商处出差,却很少相关业绩的呈现。
26、缺乏对供应商的辅导与提升。
27、供应商管理人员在供应商处有不当行为,比如中午饮酒、在供应商处办公室内吸烟等。
28、供应商管理人员的差旅费报销有明显漏洞。
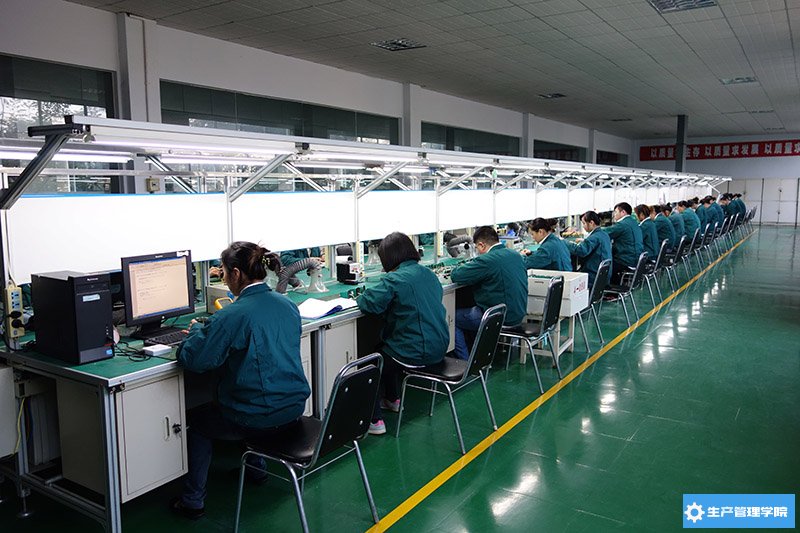
三、生产现场及安全问题点
29、现场较为杂乱。30、现场缺乏可视化。
31、现场缺乏提倡员工改善或吸纳改善意见的氛围。
32、现场安全标识不到位。
33、现场存在安全隐患。
34、现场的危险源未充分识别,并据此制定相应举措。
35、对员工的安全培训不充分。
36、以往发生安全事故,未充分梳理总结及展开教育,存在再犯可能性。
37、缺乏关于安全管控的流程或制度规定;或这些规定的有效性已大打折扣。
38、现场关于安全的可视化不充分,比如安全知识、安全制度、安全管理方法、安全事例的分析等宣讲不充分。
39、现场缺乏对日常安全工作的有效性监控。
40、缺乏安全方面的专职人员。
41、负责安全方面的专职人员技能与意识尚不足够。
42、现场无法直观探知到生产的产品及其状态。
43、员工更多敷衍来填写“设备点检表”等表格。
44、在大多数人眼里,只知日常作业,却忽视改善的重要性。
45、缺乏晨会的沟通,或晨会效率太低。
46、现场基础性管理存在不足,比如班组管理、5S管理、标准化、人员培训等。
47、现场存在不合理的等待浪费。
48、现场存在大量半成品堆积现场。
49、现场缺乏“快速反应机制”,以至于发生状况时,解决速度太慢。
50、现场的问题有“一犯再犯”的状况。
51、过大批量的生产推进方式,以至于换产品生产时,无法及时消化在线库存。
52、现场缺乏关于区域划线及标识的基准,导致划线或标识混乱。
53、现场可视化看板缺少及时的更新。
54、现场可视化看板缺少美学,布局混乱,或缺少对比化。
55、现场基础设施缺乏必要的维护。
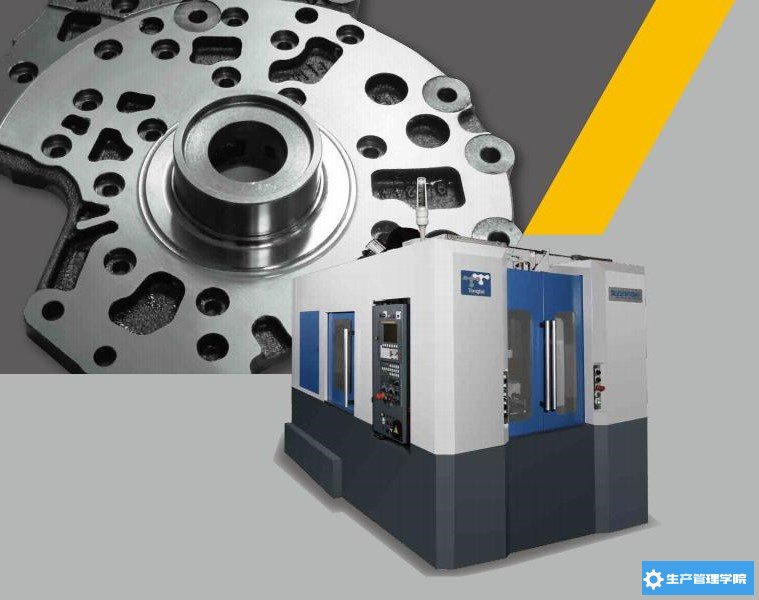
四、生产设备及作业指导书问题点
56、设备存在跑冒滴漏状况,却无人问津。57、设备缺乏关于微缺陷的识别,并进行改善。
58、不善于运用工装来提升定位等工作效率,且存在一定安全隐患。
59、设备的专业维护缺乏,导致设备劣化快于常速。
60、模具切换或生产转型存在时间上的浪费。
61、设备的备品备件管理是一笔糊涂账。
62、某些备品备件的领用并未及时入账。
63、现场有作业指导书,但离实际操作还有很大距离。
64、作业指导书未及时更新,很多信息已不再实用。
65、作业指导书缺乏对员工意见的吸纳。
66、作业指导书缺乏专业性的优化,比如缺乏动作优化等
67、作业指导书存在与其他文件相冲突的现象
68、作业指导书缺乏必要的图示化说明
69、作业指导书过于繁杂,不便于悬挂或放置于现场供员工阅读。
70、文件管控存在疏忽,有使用旧版本图纸或文件的状况。
71、设计人员存在慵懒现状,将公差设定为“一刀切”,提升了不必要的加工难度。
五、质量检验及客户服务问题点
72、首样检验等数据未及时填入记录,而后仅根据记忆将数据填入。73、检测的设置过多地依赖人员的主观性。
74、抽样比例设定存在不切实际的要求。
75、缺乏如极限样板、不良示图等易于让员工做出判断的基准。
76、测量数据存在人为的作假现象。
77、现场不良品存在标识不充分现象。导致需要再次测量才能明确不良状况。
78、不良数据未充分汇总,并作必要分析。
79、未针对重点不良,进行进一步分析与改善。
80、出货检验文件等未根据客户反馈进行及时的更新。
81、对客户的质量投诉,未优先使用“防错法”进行改善。
82、对客户投诉的回复,存在敷衍现象,且纠正措施有不到位现象。
83、负责客诉的人员一人应付,缺少组成团队,运用工具,按照步骤,对问题的深入纠正与预防。
84、对客户的紧急状况申请置之不理。
85、出货检验文件未根据客户反馈以及实际不良状况进行更新。
六、生产管理者管理的问题点
86、对员工关心不够,导致员工缺少归属感。87、存在主管人员蛮横无理状况。
88、主管传递信息不到位,员工常得不到应得到的信息,比如加班安排、客户反馈等。
89、过于依赖标语口号的激励作用,忽视日常管理的深入开展。
90、管理人员缺乏现场意识,较少进入现场发现问题。
91、管理人员未理解改善的重要性。
92、管理人员未掌握恰当的改善工具。
93、管理人员经常打击下属的改善建议或激情。
94、管理人员缺乏对自己及部门工作的规划。
95、管理人员在提升下属能力方面做得还不够。
96、管理人员未明确对下属的工作要求。
97、管理人员失于对员工实际工作的考察,导致浮而不实的人获得赏识,而务实工作的人却被冷落一边。
98、管理人员不善于运用机制化提升管理,更多的是零星的碎片式样的要求或强调。
99、管理存在随意性,比如发现员工问题,随意罚款一个金额,缺乏机制或规则的支撑。
100、存在用人不当现象,将不合格的人或懒散的人置于一个关键岗位,以至于打击员工士气,或使得某些工作难以推进。
101、人员离职率过多。
102、员工加班不做事,依赖于加班提升自己的收入。
103、过于崇尚惩罚措施,员工缺乏归属感。
104、优秀人员缺乏升迁的通道。
七、生产流程及制度问题点
105、表格过多。106、存在无需再收集数据的表格依然在使用,浪费员工时间。
107、人员工作不均衡,有人忙有人闲。
108、计件工资不合理,导致某些产品员工不愿做。
109、流程性文件制定后,疏于向员工进行宣导,以至于很多人不知道有这份规定的存在。
110、企业办公室杂乱不堪,不利于整体5S管理的氛围形成。
111、企业对表现不佳者,采取了过于包容的态度。
112、会议存在明显的扯皮或踢皮球状况。
113、会议制作的措施无人跟进,落地乏力。
114、企业执行力堪忧,不开会议无法推动工作。
115、部门隔阂严重,管理者只管扩充自己地盘,忘记企业本源的追求。
116、企业在人事任命上,过于随意,以至于人员缺少稳定感。
117、业绩考核时,与实际状况存在较大偏差。
118、每年年底时,缺少对第二年工作的相应规划。
119、缺乏有魄力的领导者来推进现状的改变。
120、领导者因自身能力的缺乏,而不怕招有能力的人进入企业。
121、领导者缺乏了解员工真实想法的渠道。
122、领导者疏于对市场趋势的掌控,在即将淘汰的产品上作了过多的投资。