精益管理是中国制造业提升的必经之路,而欧美日的自働化历程,是中国企业未来的方向,依托精益生产,实现自働化生产,优化业务流程,整合产业链的服务。
精益生产是以自働化(Jidoka)和准时生产(JIT)为支柱的。这里所谓的自働化是智能型的自働化。通过精益改善,建立连续流,按节拍生产。而精益自働化的目标就是要配合产线节拍,从自働化层面来优化连续流,减少人员作业、取放、传递与判断等浪费,实现人机分离;结合快速切换、防呆等精益技术,适应柔性生产,同时,通过目视化、信息化、异常响应等技术的应用,优化和简化管理活动,实现安全自働化、工具自働化、工程自働化、生产线的自働化、整个工厂的自働化。
要做好安全自働化可分以下6个步骤来实施:
第一步:全员确立安全第一的理念,所有人必需明确安全生产是制造的基础,始终应将它摆在第一位。
第二步:消除不合理,不均一,不必要的浪费。
第三步:作业标准化,人的工作与机器的工作须确实区分,在设备的危险区域内不能有人。
第四步:推行6S即整理,整顿,清扫,清洁,素养和教育。
第五步:有异常自働停止。
有了安全自働化为基础,接下来我们可以着手以装配工程为对象的工具自働化。装配工程包含7个働作:寻找,搬运,决定位置,取道具,锁紧,道具还原,检察等。若将每个働作一一赋与智能使其自働化,则有工具自働化的8项步骤如下:
1、工具道具化:将市面上所卖的工具加工为道具即专用化的工具,以方便使用。
2、位置复原:作业完成后道具及小设备回复原位置。
3、成组化:于一定作业位置,将所须的道具及配件成组,准备齐全。
4、选择自働化:作业,道具,配件等,不必经过考良,寻找及选择,而能够规律进行的状况。
5、道具自働化:由道具所进行的工作,转由电力或空压等小设备进行。
6、决定位置:决定道具,小设备的使用位置。
7、输送自働化:道具小设备的工作,与作业者的工作有所区分。
前面所提到的安全自働化基本项目,即在机械加工时,若发生任何异状时,能够自働加以阻止。有了这个安全保障的基础就可以依以下10个步骤逐步实现工程自働化:
1、自働夹具:加工配件的固定,以机械,油压,气压等自働方式进行。
2、自働加工:手働加工作业以机械,油压,气压等自働方式进行。
3、自働搬运:弹出的配件自働搬运至次工程位置。
4、自働测定:配件全数自働测定。
5、自働输送:手働输送作业以机械,油压,气压等自働方式进行。
6、自働停止:加工工具及主轴等在加工完成时自働停止。
7、自働回复原位置:加工工具及主轴等在加工完成时自働停止后,返回启働点。
8、自働弹出:加工完成后配件自働卸下。
完成以上十步骤,就可以完成人与机器的作业分离,作业员只需做装夹,拿取工件的働作即可,从而为一人多机,少人化创造了条件,同时质量也会得到很大提升。因为机器出错的机率肯定比人员手工作业小得多。
安全自働化是基础,工具自働化以装配作业为对象,工程自働化以机械加工工程为对象,综合以上三者,以降低制造成本为目标,从生产上的“点,线”普升至“面”改革水准。接下来所要做的就是生产线的自働化。生产线的自働化有以下步骤:
1、先确定节拍时间:不论何种制品,皆在其必须完成的恰好时间内制造。
2、控制:只有当后工程无产品,而前工程有产品的情形,才进行工程。
3、灯号:传达生产线流程中产品异状的装置。
4、单位流程:只针对一项产品,进行单位配件的搬运,装配,加工及素材的领取。
5、先导器:制作以目视即能了解节拍时间的装置。
6、U字型生产线:将设备依工程顺序逆时针排列,并由一人负责出口及入口。
生产线实现了自働化就实现了自働化的点线面整合,接下来通过以下5步骤就实现了整个工厂的自働化:
1、水蜘蛛:分批的向各生产线领取,供给即巡回混载搬运人,情报传达人。
2、看板:消除制造过多的浪费,而且附有降低成本的自働指示装置等道具。
3、出货货品齐全:能否建立与消费者制造厂邻接的关系,其中以异状探测为第一优先。
4、目视管理:工厂所有物品的正常状态,异常状态,瞬间能清楚。
5、大空间化:结合各生产线的零头作业,成为整数的作业,以进行少人化。
将丰田自働化方式应用于生产现场可达到的功能包括:
导入自働化模式可以从源头做到不生产不良品、不流出不良品的效果,使不良品无法通过生产线,一旦制程发生不良品或条件异常的情形,能够透过安灯(Andon)、目视化管理板、声光警报信号等装置立即反映异常状况,若是异常状况持续产生且一时无法排除则产线立即停止,现场相关人员包括:主管、作业人员及相关部门人员(如品保、IE、设备保全等)都必须立即面对问题、调查原因,并采取临时性与永久性的对应措施,以防止相同的问题再次发生。如此,不但能彻底有效地解决质量异常的真因,同时也将生产线塑造为具备「自律神经」的机能,一旦发现任何问题,相关部门人员自动自发负责地实时解决,而不是要等到事后统计与开会才去对应处理,更不需要经营管理者时时的监督与管制,这也是生产管理的理想境界。
传统的自动化设备因为无法有效检知异常状况,因此还需要派人去监管机器,在机器设备正常稼动时,人力资源反而形成了浪费。符合自働化定义的生产设备因为安装了感知装置以及防错防呆机制,针对产线的实际生产数量、良品条件变异、设备的操作状态做到实时化管理。在此条件下,人员不需要当机器设备看守者,从而实现了「人机分离」的结果。并且,搭配「多能工」的培训机制与标准作业,一个作业人员可以同时操作或管理多台机器设备,进一步实现了「一人多机」的模式,将生产线的人力、设备、物力等资源做到合理配置,达到资源运用的最大化。
具备自働化模式的生产线与设备能够稳定地制造客户所需要的产品,在确保质量无虞的前提下满足生产计划所订定的目标,避免产出的过剩库存品,亦即将产线改造成更为紧致、仅需投入更少资源的优化模式。目前制造业厂商已经面临来自客户的少量化、多样化、短交期化订单需求的压力,唯有在自働化的基础下实践JIT生产模式才能因应未来多变的市场挑战。
自働化 V.S 自动化
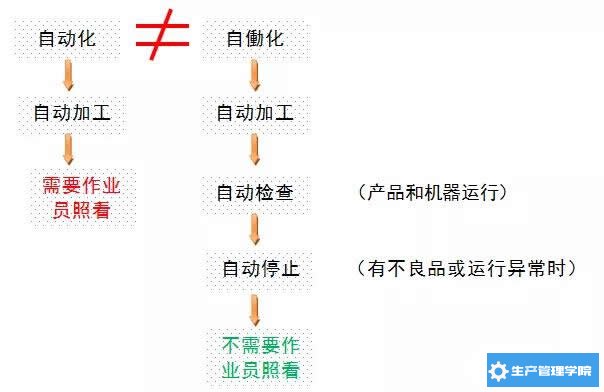
而自働化的基本功能之一就是发现不良品就停机,从而防止不良品流入后道工序。
准时制其实是要求整个流程上的所有步骤都要同步协作(按同一节拍运作),以达到“大家好才是真的好”的效果。
准时制的效率也只有在每个步骤都协作良好的情况下才会有最佳的结果。
因为,制程上单个工序或步骤的出类拔萃对整体效率其实没有太大的正面影响。
类似的可以参照木桶中的“短板理论”,或生产管理中常见的“瓶颈工序”。
自働化其实是要求每个工序都需要有识错,防错,快速修正的能力。
如同接力跑,队员之间的协作固然相当重要,但个体之间弱爆了,竞技的结果也是一败涂地。
中国队可以通过协作跑赢日本队,但碰上美国队基本没戏。为什么,个体之间的差距太明显。
但有时,单纯从表面上看,自働化跟准时化之间似乎有自相矛盾的地方。
准时化把各道工序间的物流看成是河流,尽量使其没有浑浊的地方,将其改善为没有时间差,没有浪费的物流。
确实,在自働化的机制下,问题一出,机器噶然停止,生产瞬间归于沉寂,物品流转怦然就而段。
后道工序催货催得要死要活的,你倒好,灯一亮,声一响,说不干就不干了。
自働化在一定程度上是阻止了物品的流通。但首先要看它阻止的是什么样的物品。
不良品流通到哪里都不能带来价值的增加,除了增加后道工序的处理难度和成本之外,也就是更大的浪费,对企业的正效应贡献完全没有。
而在自働化体制下,停止机器(生产线)是为了使问题得到迅速的解决,以免残留到后面的工序。
从另一个意义上来说,一个制程,无论用什么理念或武器武装起来,如果不能避免交付不良品,那就是基本要求都不能满足。就如一个走路都不文档的人,你用博格特的方法去训练他也不可能快得起来。
而一发现问题就识别出不良品,停机改善,就可以向顾客保证质量。
所以,自働化确实是实现准时制生产的核心基础之一。
Build in quality. 产品质量来源于制造这一观点在大部分企业内都被提倡。
可实际上很多企业在做产品检查时都疏忽了这一点,无论多么努力在生产后做检查,都不会产生附加价值,只不过产生了更大的浪费。
所以在自働化体制中,坚持贯彻的是“不生产不良品”,而非“发现不良品” 。
因而,从根本上来说,自働化的核心就是丰田生产方式的核心思想:
——发现问题就停机,避免生产过多不良品而导致浪费;
——发现问题就停机,避免不良品流入后道工序而导致其他浪费;
——发现问题就报警,通过及时处理避免等待和停工的浪费。
自动化机械具有高性能化和高量产化,如果没有异常识别,报警和停机系统,在发现不合格产品之前就会生产出大量的不合格产品,从而导致大量的不良品浪费。
同时,根据牛鞭效应,供应链上任何异常都会在后端进行逐级放大。
如果不在问题刚发生的地方和第一时间就处置妥当,后续的处置措施就会越来越难,成本越来越高。
而在自働化体制下,在瞬间就可以发现不合格产品,从而防患于未然。
同时,自働化的状态下,一旦产生不合格产品,就会立即停止生产线并进行改善活动。
通过彻底实施改善,可以建立起没有浪费且更加有效的生产体质。
而传统模式下,继续运转机器,先取得不合格品的数据,做一些分析,再去实施改善,这样改善就滞后了。
很多没有停止生产线的企业因为没有培育一种停止了生产线后能迅速进行改善的体质,从而在改善和继续运转机器的时候,产生大量的浪费。
单从问题解决的效率上来说,自働化也有无法比拟的优势。
试想一下,警察是在案发的第一时间就在案发现场抓住凶手容易一些?
还是在案发多时之后,根据大量物证,人证,访谈等各类信息中的蛛丝马迹来抓住真凶更容易一些呢?
而自働化就是要求人们必须在报警时第一时间奔赴现场查找“真凶”并解决问题的机制。
所谓自働化就把重点放在阻止不良品的流动,当发生异常状况时,生产线会自动停止的生产结构体系。
试想一下,车间内前一秒机器隆隆,一瞬间陷入死寂,然后一大群人无所事事,隔岸观火。
时间一分一秒过去,机器还在安静的看着你,一大群人在车间里游荡。
我想,这时如果是按你的要求而停的机器,时钟滴滴答答的敲在你的心头,你很大概率是不会有岁月静好之类的感悟的。
这类事情多了,想不走人都难!并且,没有人会同情你。
——先制定完备的停线方案和解决问题程序;
——然后将人员一 一合理进行分工;
自働化体系下,停线后的快速解决问题才是根本中的根本!
7. 建立清晰,明了的报警系统(不能依赖广播系统)。
8. 建立问题解决的程序和时间要求(如现场主义)。
11. 建立流程绩效指标(质量考量作为第一个重要的指标)。