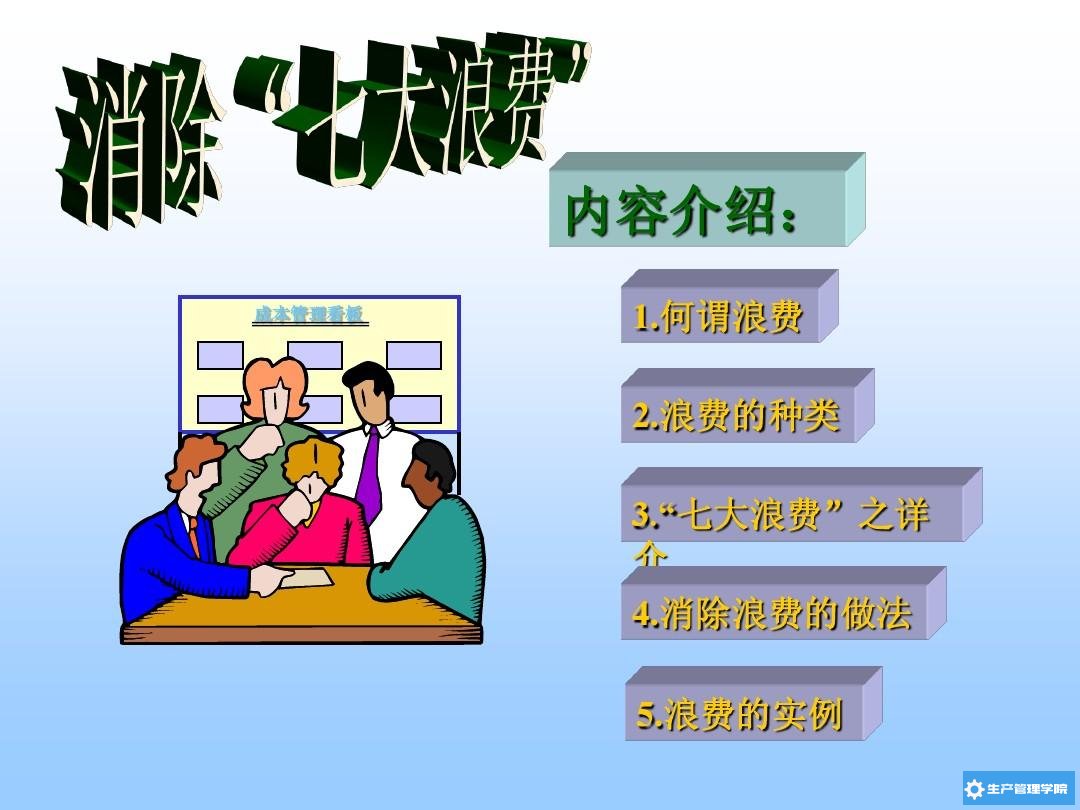
降低成本的唯一办法——消除浪费!本文您將了解什麼是七種浪费,是什麼原因造成的,以及它們可能給組織造成的損失。您還將學習如何使用看板和5S之類的工具來處理每種浪费。
1、缺陷的浪费
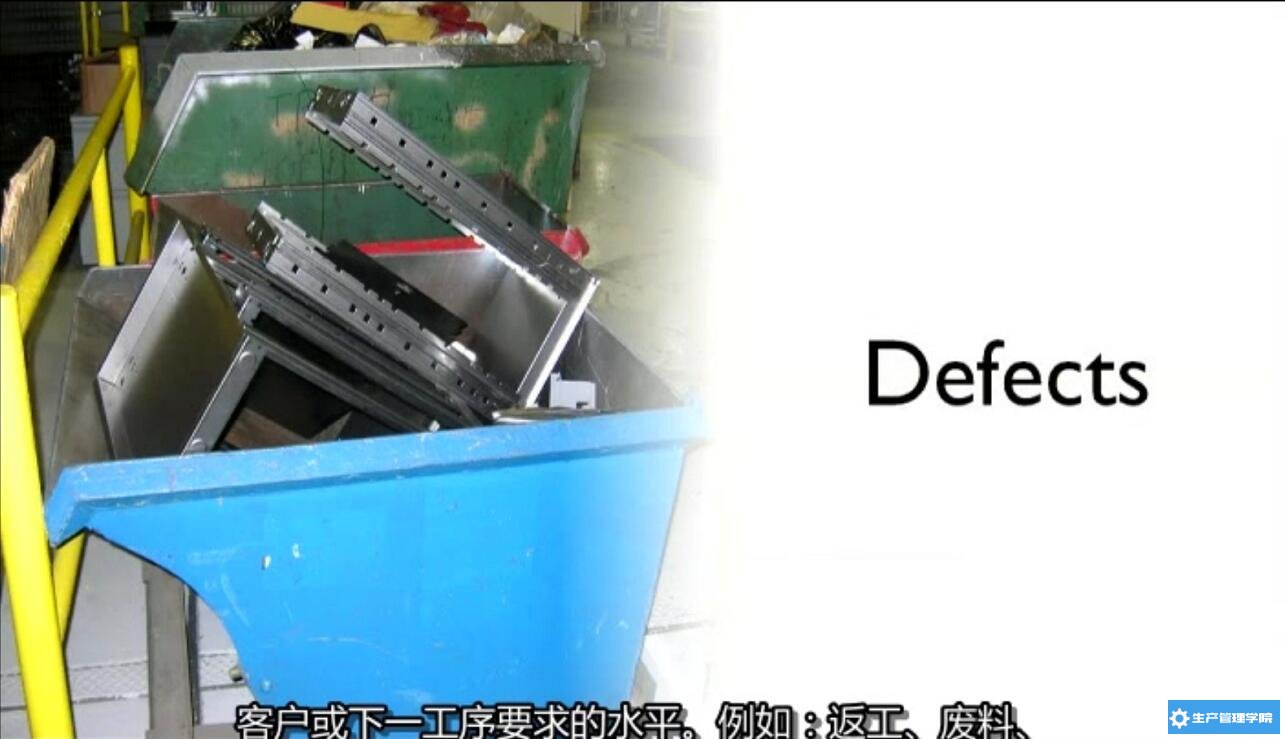
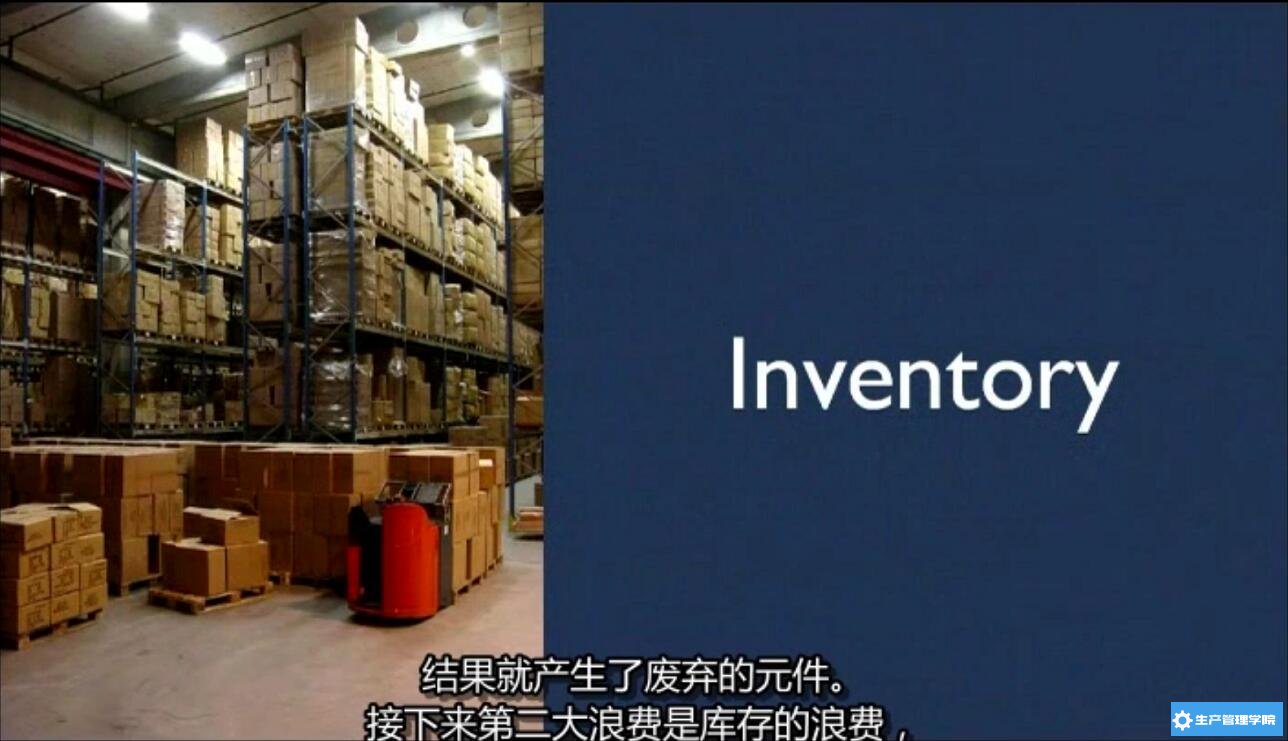
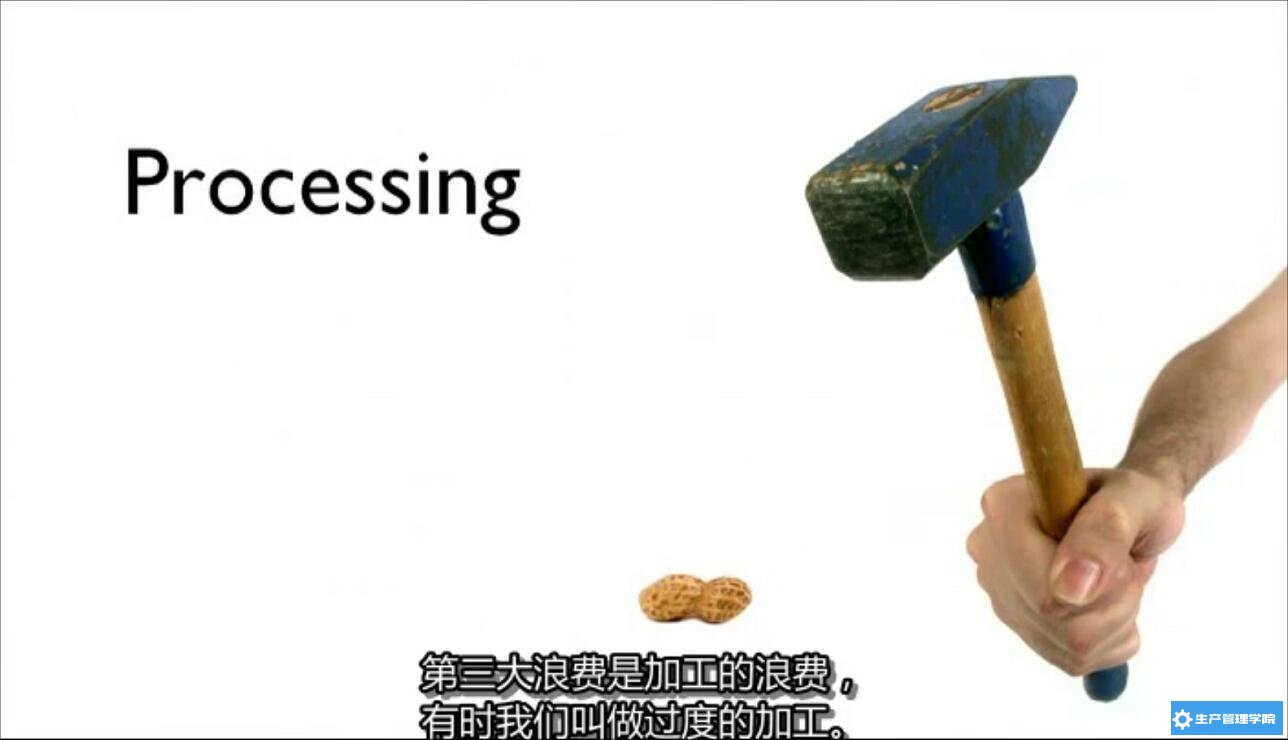
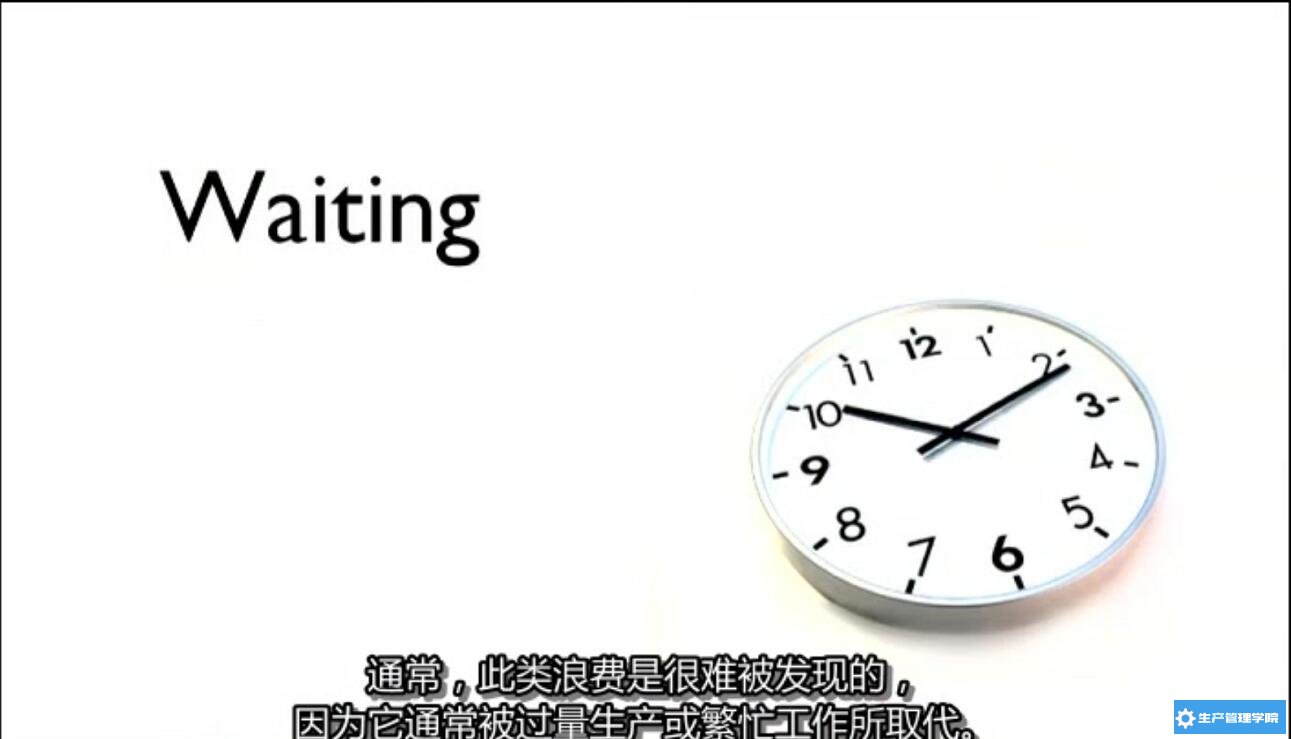

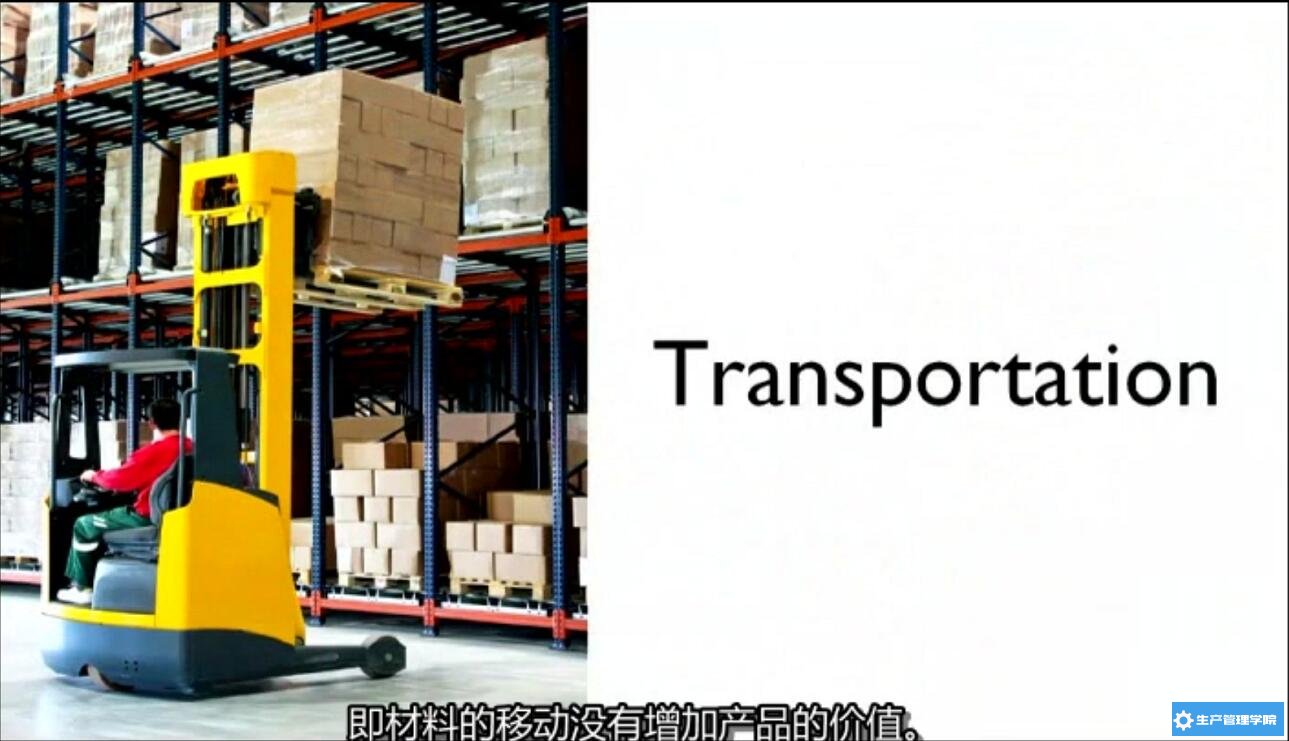
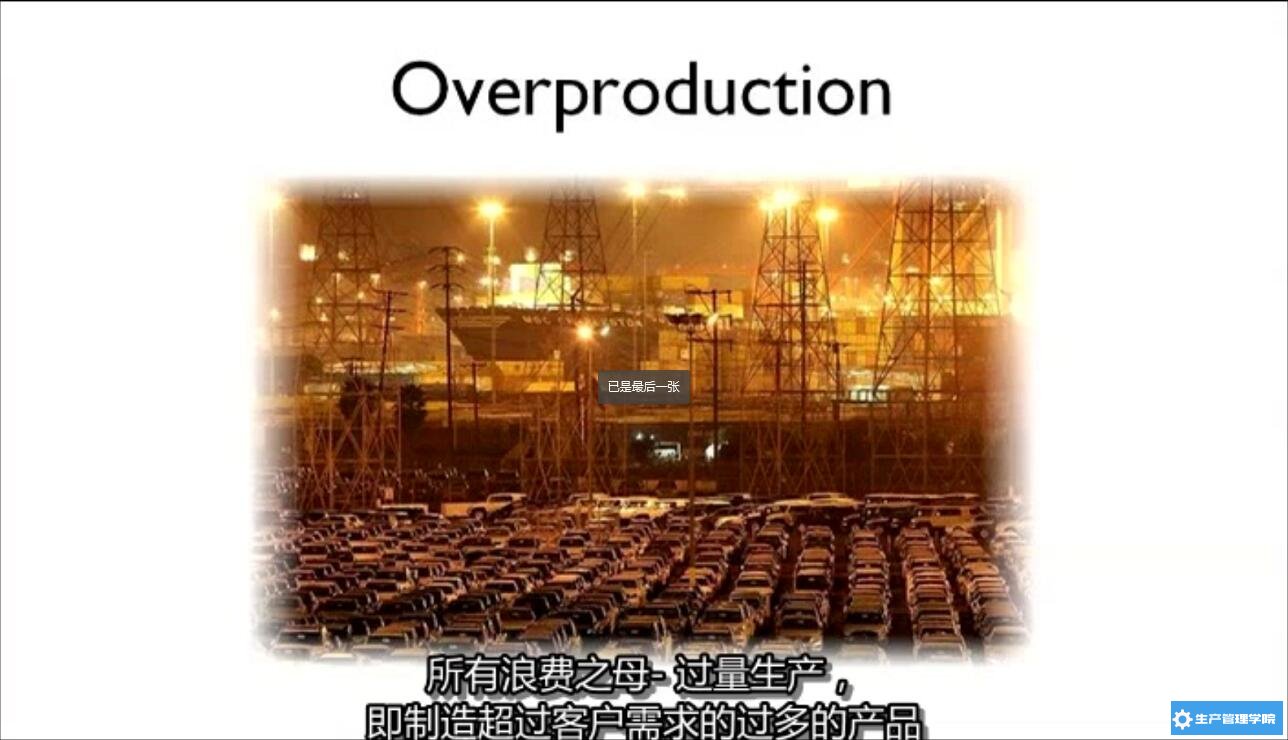
1、生产过剩的浪费
生产过剩的表现形式
2、库存的浪费
3、搬运的浪费
4、等待的浪费
5、动作的浪费
6、加工的浪费
③ 最终工序的修正动作;
④ 频繁的分类、测试、检验;
⑤ 多余不必要的标记。
上一篇:价值流图的特点
下一篇:大野耐一在丰田的改善历程
什么是SOP?所谓SOP,是 Standard Operation Procedure三个单词中首字母的大写 ,即标准作业程序。(1)是以文件的形式描述作业员在生产作业过程中的操作步骤和应遵守事项;2)是作业员的作...
Andon系统(中译安灯或暗灯系统)源自丰田公司,是一款重要的车间现场管理目视化工具。Andon系统汽车公司,用来实现“立即暂停制度”,以即时解决质量问题(而不是下线返修),达
当今,各种生产管理方法论从丰富到泛滥:精益生产、敏捷制造、6ð、5S、TPM、SPC、8D、QCC、TOC、阿米巴经营、绩效管理、指导书、文件、标准、报告、会议、培训、评比等。本课程是授
对产品或零件加工制造全过程中加工、检查、储存、等待和搬运所进行的分析。获得生产流程、设备、方法、时间等方面的资料,以便制定恰当的生产计划;为进一步制订改进方案提供