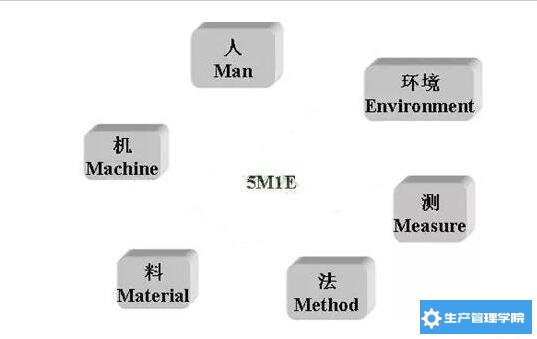
什么是5M1E?
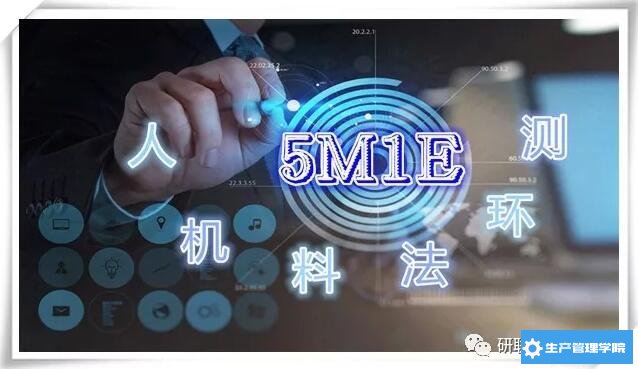
造成产品质量的波动的原因主要有6个因素:
a) 人(Man/Manpower): 操作者对质量的认识、技术熟练程度、身体状况等;
b) 机器(Machine): 机器设备、工夹具的精度和维护保养状况等;
c) 材料(Material): 材料的成分、物理性能和化学性能等;
d) 方法(Method): 这里包括加工工艺、工装选择、操作规程等;
e)测量(Measurement):测量时采取的方法是否标准、正确;
f) 环境(Environment): 工作地的温度、湿度、照明和清洁条件等;
由于这五个因素的英文名称的第一个字母是M和E,所以常简称为5M1E。6要素只要有一个发生改变就必须重新计算。工序质量受5M1E即人、机、料、法、环、测六方面因素的影响,工作标准化就是要寻求5M1E的标准化。
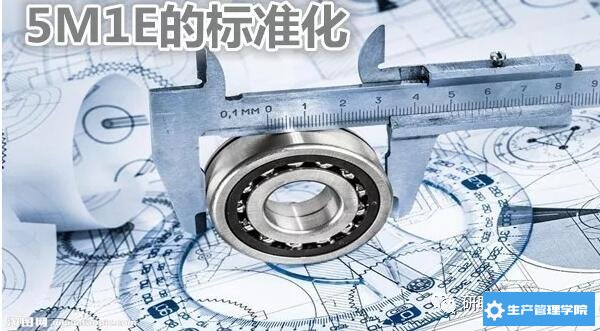
01、5M1E简介
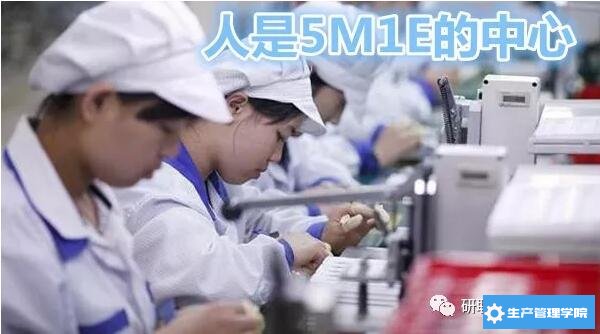
1、质量意识差;
2、操作时粗心大意;
3、不遵守操作规程;
4、操作技能低、技术不熟练,以及由于工作简单重复而产生的厌烦情绪等。
控制措施:
1、加强“质量第一、用户第一、下道工序是用户”的质量意识教育,建立健全质量责任制;
2、编写明确详细的操作流程,加强专业培训,颁发上岗证;
3、加强检验工作,适当增加检验的频次;
4、通过工种间的人员调整、工作经验丰富化等方法,如多能工,消除操作人员的厌烦情绪;
5、广泛开展TQM活动,促进自我提高和自我改进能力。
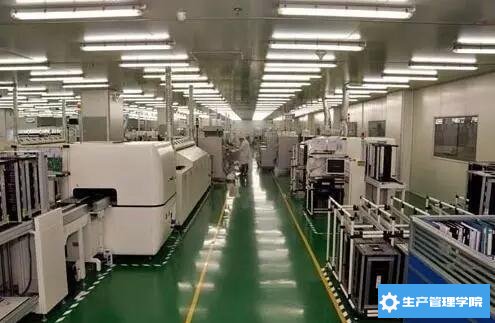
1、未定期及时点检、保养和维护造成的设备故障引发缺陷;
2、缺乏首件检查,造成批量缺陷;
3、工人工作的疏忽,造成的缺陷。
控制措施:
1、加强设备维护和保养,定期检测机器设备的关键精度和性能项目,并建立设备关键部位日点检制度,对工序质量控制点的设备进行重点控制;
2、采用首件检验,核实定位或定量装置的调整量;
3、尽可能培植定位数据的自动显示和自动记录装置,减少对工人调整工作可靠性的依赖。
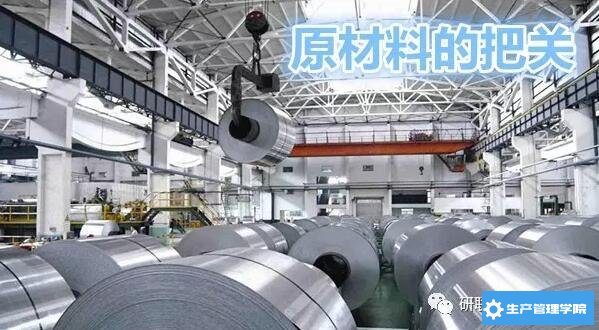
1、原材料来料不良;
2、供应商质量不稳定;
3、原材料进场前缺乏必要的检验和判定。
控制措施:
1、在原材料采购合同中明确规定质量要求;
2、加强原材料的进厂检验和厂内自制零部件的工序和成品检验;
3、合理选择供应商(包括“外协厂”);
4、搞好协作厂间的协作关系,督促、帮助供应商做好质量控制和质量保证工作。
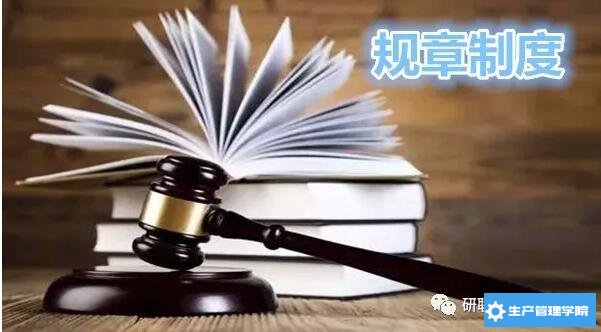
1、加工方法,工艺参数和工艺装备等正确性和合理性;
2、贯彻、执行的严肃性。
控制措施:
1、严格首件检验,并保证定位中心准确,防止加工特性值数据分布中心偏离规格中心;
2、培训,使操作人员熟悉定位装置的安装和调整方法,尽可能配置显示定位数据的装置;
3、加强定型刀具或刃具的刃磨和管理,实行强制更换制度;
4、积极推行控制图管理,以便及时采取措施调整;
5、严肃工艺纪律,定期工艺检查制度;
6、加强工具工装和计量器具管理,做好周期检查和计量器具的周期校准工作。
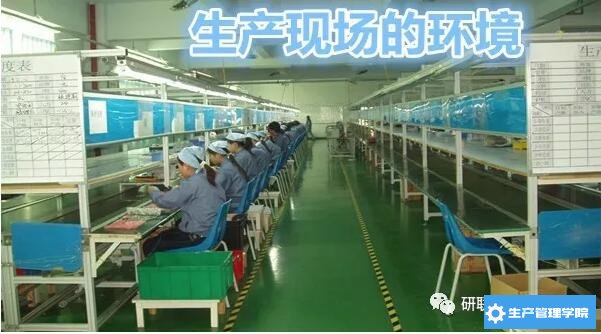
“环”指生产现场的温度、湿度、噪音干扰、振动、照明、室内净化和现场污染程度等。 在确保产品对环境条件的特殊要求外,还要做好现场5S的整理、整顿和清扫工作,大力搞好文明生产,为持久地生产优质产品创造条件。
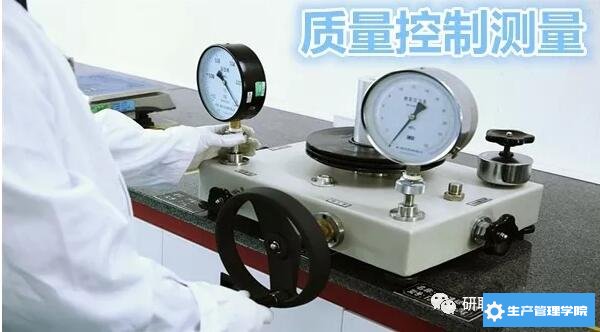
1、计量器具的选择,包括量程、计量精度等;
2、定期的校准、和调整;
3、计量器具的校准规程和统一管理。
控制措施:
1、确定测量任务及所要求的准确度,选择合适准确度和精密度能力的测试设备。
2、定期对计量器具进行确认、校准和调整。
3、规定必要的校准规程。包括设备类型、编号、地点、校验周期、校验方法、验收方法、验收标准,及问题应急措施。
4、保存校准记录。
5、发现测量和试验设备未处于校准状态时,立即评定以前的测量和试验结果的有效性,并记入有关文件。
02、5M1E应用
03、从5M1E到5MTE:生产管理的第七要素
第七要素—时间
实际上,在以往对于现场管理的要素研究中,已经逐渐认识到时间重要性。比如,在现场管理六大指标中,Q(质量)D(交货期)C(成本)M(士气)S(安全)E(环境)中的D,其实就是时间的概念。
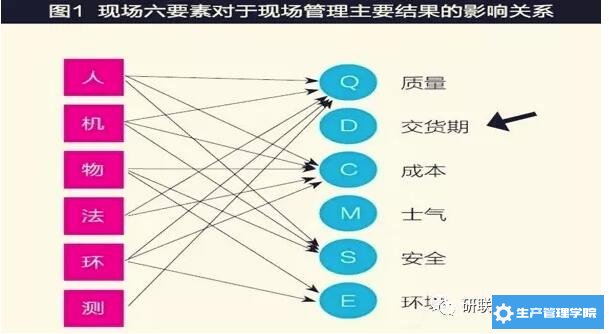
图1标明了现场管理的六大要素对于现场管理结果的影响。可以看出,5M1E的六个要素对于QCMSE等结果指标都直接产生影响,而D(交货期)指标,是由时间(TIME)决定,而不是由这几个要素直接决定的。很明显,有必要在5M1E模型中补充第七要素一时间。这样,才能解释对于现场六个关键结果的影响。
在现场管理中,时间的概念远远不止于交货期这么简单。实际上,现场时间是现场最重要的资源之一。能否对时间进行有效的管理,将决定现场是否能够取得管理上的成功。比如,很多公司会将合同履约率当成现场管理的考核指标之一。由于没有时间要素的要求,这一指标的考核并不能促进履行合同的能力的提高。如果企业将合同履约率改成合同交付时间或者周期,则能够更好地反应企业的交货能力。另外,在计划经济时期,我们常常听到的超额完成生产任务,其实是提前完成了生产任务,在短缺经济情况下还不至于对现场管理造成严重影响。但放在当今的市场经济环境中,如果企业过多或者过早地生产,就会造成库存,搬运等大量浪费。
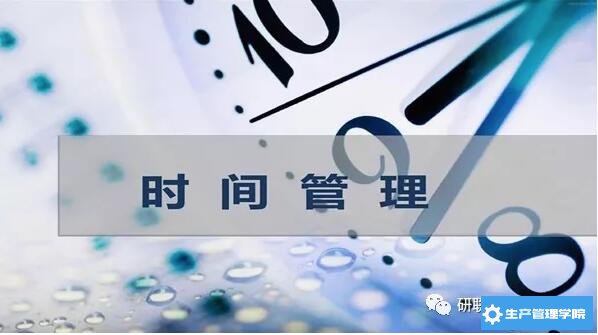
5MTE模型
实际工作中,5M1E的六个要素,基本上都和时间要素有着密切的关系。所以,非常有必要把时间这一要素提出来,作为模型中一个单独的要素,才能提示广大的现场管理人员对于时间的重视和分析,而不是忽略如此重要的要素。
我们构建的5MTE模型把T(时间)置于其他六要素的外围,而不是放在尾端,是为了强调T并不是一个末位的要素,而是一个至关重要的要素。同时,为了强调T与其他六要素不是截然分开的关系,而是相互包含和渗透的关系。
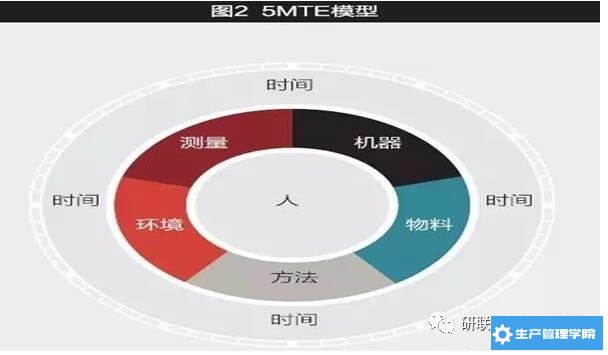
以下是5M1E(人、机、物、法、环、测)与T(时间)要素的关系分析。
人——时间
现场管理进行“人”的要素分析的时候,有一个重要的分析工具——人工工时,就是关于时间因素的管理。至今,有很多企业仍在依靠工时定额的传统方法来计算效率、成本、薪酬。
为了提高工时利用率,管理者们研究了很多方法。从科学管理之父泰勒的铁锹实验开始,到后来吉尔布雷斯的动素分析,到动作时间研究的MOD(以手指动弹的时间作为基本单位,其他动作以手指动作的整数倍来表示,lMOD=0.129s,手指移动2.5cm的时间)方法,其本质都是通过分析人的动作特征来提高工时利用效率。
尤其是对于基层的作业者而言,企业所付的薪酬其实就是用来购买作业者的劳动时间。
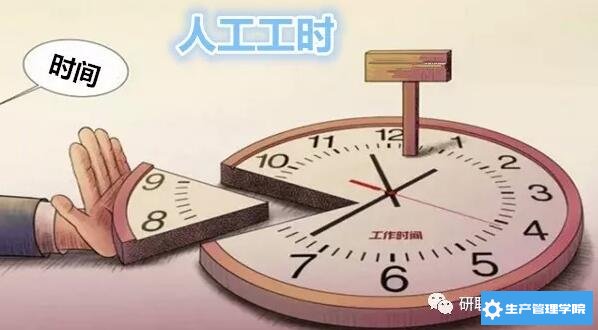
机——时间
OEE=时间利用率*设备性能率*产品合格率
其中,时间利用率=(负荷时间-停机损失)/负荷时间*100% =(有效)利用时间/负荷时间;
设备性能率=(生产产品数*设计速度)/利用时间*100%;
产品合格率=(生产产品数-不合格品)/生产产品数*100%。
OEE本质上是设备有效利用时间占设备总时间的比率,表现为有效时间与总时间的比率。了解OEE指标,可以使管理者能够对于当前的产能情况做出准确的评估,不至于做出重大设备投资的错误决策,给企业造成产能过剩,或者不及时投资而造成产能不足,错失市场机会。例如,某电器生产商领导就曾经因为产能不足而准备投入新的生产线,但经过计算,其OEE指标仅有50%。所以,该公司应该做的是提高现有设备的利用率,如把原来的两班运转改成三班运转即可,而不是再建一条高成本的生产线。如果投入新的生产线,只会造成设备的闲置,增加投资,及增加设备的维护成本。
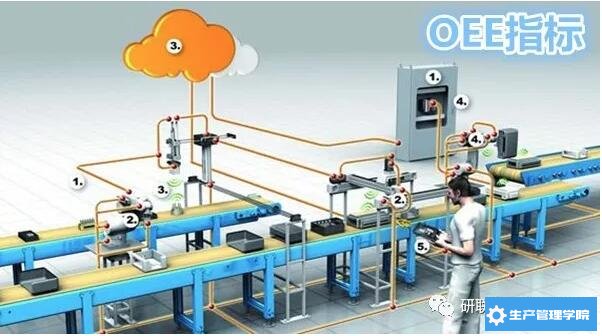
此外,MTBF、MTTR和MTTF指标也是设备管理中的重要指标,这几个指标均与时间这一要素有密切关系。
其中MTBF(MeanTime Between Failure,平均无故障工作时间),是指从新的产品在规定的工作环境条件下,开始工作到出现第一个故障的时间的平均值。MTBF越长表示可靠性越高,正确工作能力越强。
MTTR(Mean Time To Repair,平均修复时间),是指可修复产品的平均修复时间,就是从出现故障到修复的这段时间。MTTR越短表示易恢复性越好。
MTTF(Mean Time To Failure,平均失效时间),是指系统平均能够正常运行多长时间,才发生一次故障。系统的可靠性越高,平均无故障时间越长。
由此可见,在5M1E的有关“机”的各项指标,主要的测量要素就是时间。
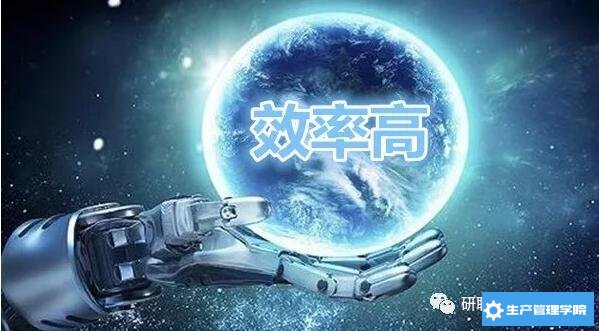
方法——时间
在典型的生产制造型企业,比如在一个冰箱的生产工厂,在组织生产时,必须实施标准化作业。标准化作业实际上是为了达到高效率而实现人机料的有效组合。在标准作业三要素里面,有节拍时间、标准作业顺序、标准手持(标准在制品)。时间又一次作为主要的管理要素排在前面,在此我们重点探讨节拍时间。
节拍时间(TaktTime) 是指各生产单元内加工—个单位的产品所需要的时间。公式为:
节拍时间=(每期的可用时间-每期的扣除时间)/一天的必需数量
节拍时间反应了生产一件产品的平均时间。通用的测量节拍时间的指标有C/T,T/T,S.T和Neck工程。
Neck工程,是指全体工艺中作业时间最长的工位。其它工位作业再快,最终生产出来的数量与Neck工位生产出的数量是一致的。
可以看出,这几个反应现场管理效率的重要指标都和时间有关。
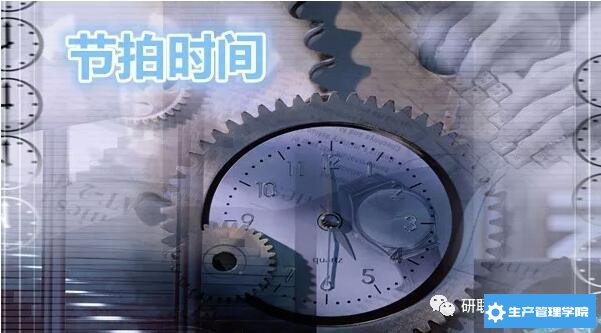
环境——时间
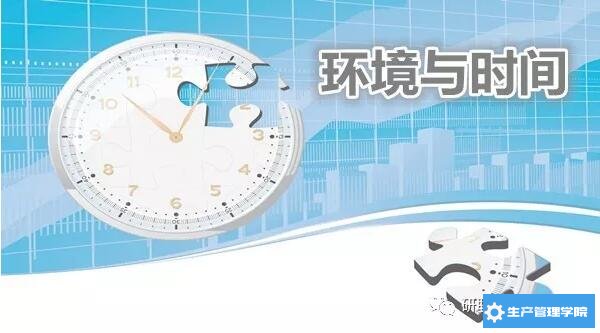
测量——时间
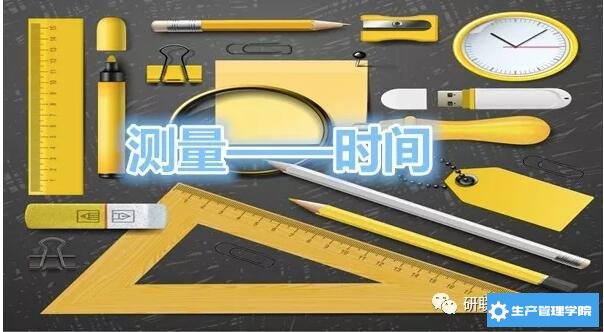