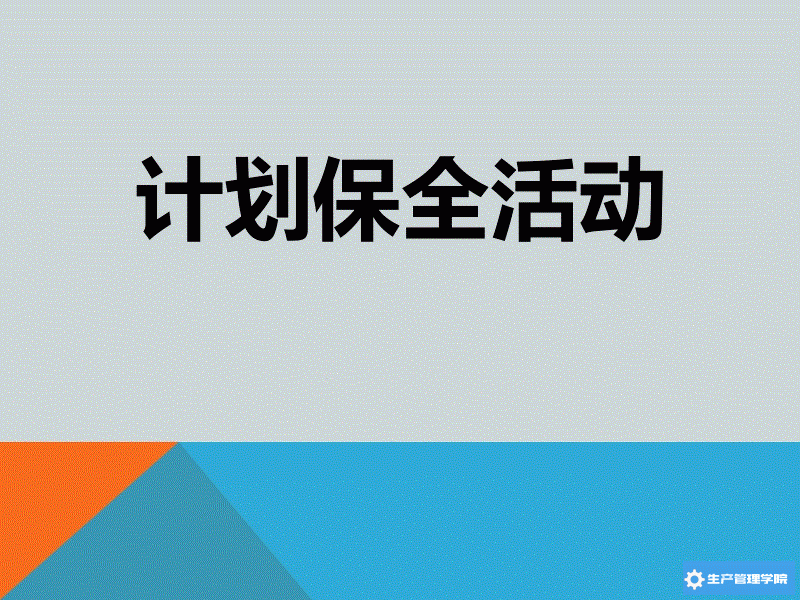
计划保全的特点
计划保全是通过设备的点检、分析、预知,利用收集的情报,早期发现设备故障停止及性能低下的状态,按计划树立对策实施的预防保全活动和积极的运用其活动中收集资讯的保全技术体系,提高设备的可靠性、保全性和经济性以确立以MP(保全预防)设计支援及初期流动管理体系。机械设备在使用过程中,会逐渐老化,出现故障,乃至发生事故,影响生产,为保持和延长其使用寿命,人们采取多种方式进行维护,如:事后维修、预防维修和预测维修等。但究竟哪种方式能达到既节省成本,又能使设备安全可靠运行呢?应当说针对不同企业的不同工况,各有优点,相比之下,设备主动维护会更被人青睐,是因为它走了一条治“本”之路。
如果一个人平时就注意锻炼身体,控制饮食,起居有常,心情开朗,心胸大度,所谓“三分治七分养”,把精力放到预防上,这个人有病的机会就较小,在设备上叫主动维护,也就是从设备设计开始到报废钧整个周期通过监测和控制故障的诱发因素,使故障苗头没有产生的因素和可能,以达到防止失效发生和发展,进而保持设备的精度和工艺性能,延长机器的使用寿命,太幅度节约维修费用。但在现实管理中往往被忽视,一是观念问题或者观念改变较慢,如有人宁肯花几万、十几万的费用用在临终抢救上,而不肯每年用几千元做一次全面体检,早发现疾病苗头,早治疗;其二是由于很多企业在整个设备管理中没有做好分析和统计,没有长期意识。主动维护虽成本相对较低,也需要时间和资金的投入,但忽视所带来将是更大的资金和时间投入,美国一些专门机构对设备液压系统几种不同维修方式所需费用做了分析和比较,认为主动维护所用成本是最低的,而计划维修是主动维护的重要手段。
计划保全的主要内容
(1)计划保全的主要方面在设备运行一段时间之后,按照既定的计划进行检查、维护和维修,这些都属于计划保全的范畴。计划保全的主要活动内容大致可分为以下几种:
①现场自主保养
计划保养和自主保养是互相结合的,自主保养是由现场操作人员进行的;计划保养是设备保养部门配合现场操作员,在故障发生前、中、后进行的一些有计划的保养。
②及早发现异常
及早发现设备出现的微小异常,将有利于设备的及时修复。一旦异常转化为故障的时候,要彻底修复设备难度就会比较大,有时候还需停止设备的运行进行修理,这样对生产的影响较大。
③保养信息收集和建立
通过保养信息系统的建立,专业维修人员和现场的工人可以建立密切的联系,专业维修人员可以快速地了懈到现场设备的运行情况和状态,进而采取掴应的保养维修措施和手段,缩短维修的时间。
④技术文件库建立
从设备的购买开始,建立技术资料库,制定保养的措施的规程,使操作人员和维修人员按照规程逐步进行保养。这种系统工程能起到事半功倍的作用。建规建档,针对每台机床的具体性能和加工对象制定操作规章,建立工作与维修档案,管理者要经常检查、总结、改进。
⑤人员合理安排和技能培训
为每台数控机床合理分配专门的操作人员、工艺人员和维修人员,通过保养的实施使所有人员不断地努力提高自己的业务技术水平。
(2)保养计划的编制
在计划预维修中,设备的维修是通过计划实现的,因此维修计射准确与否直接决定了其维修或保养的有效性。因此在编制计划时应依据以下原则:
①结合设备运行动态管理
设备运行动态管理是指通过一定的手段,使各级维护与管理人员能牢牢掌握住设备的运行情况,依据设备运行的状况制定相应措施。
a.通过对设备进行的日常和定期点检、定期技术普查测定等,对设备的技术状态进行分析,以此验证设备的实际技术状态及维修间隔的长短,从而提高设备维修计财的准确性、合理性和经济性。
b.建立健全巡检保证体系,在现场设备管理中,除操作人员负责对本岗位使用设备的所有巡检点进行检查外,还应依据设备的多少和复杂程度,配备专职巡检人员,专职巡检人员除负责承包重要的巡检点之外,要全面掌握设备运行动态。
c.设备状态信息建立、传递与反馈。在巡检时对发现的毒般隐患或缺陷,应做好记录检查后登入检查表,根据故障和隐患的类别由相应的管理人员及时安排处理,以此为依据作为计划编制的重要基础。巡检中发现的设备缺陷,必须立即处理的,由生产和设备管理人员及时组织处理;其他可在确定控制方案和处理方案后,纳入检修计划。
②结合设备的技术改造规划
从企业设备构成和技术装备水平出发,采用新技术、新工艺、新材料,结合修理进行技沭改造,有效的利用修理时间和维修资金,提高企韭豹技术装备水平。
③同生产计划的协调
维修应服从生产计划的需要,必须考虑到对生产计划的影响,权衡经济效果。
④修前预检
对于年度检修计划或季度维修计划的项目,在计划实施前对其进行预检,确认其和计划的符合程度并根据实际情况做出调整。
(3)实施设备计划保养管理的基本条件与应树立的观念
①实施计划保养应具备的基本条件:
获得各级管理人员的支持、配备专业技能的保养人员、树立正确的设备观念、生产及管理部门和人员间的无边际充分合作、有完善的设备技术和状态资料、保持完整的报表与记录。
②作为推行设备保养,应该树立以下观念:
设备的损失包含故障损失和管理损失;应是防止故障而非统计故障;设备的维修管理以成本及绩效为基础,采用培育人才及具备工作价值的工作环境;加强维修、管理体制及技术;积累并强化设备技术(体质);落实日常预防防管理、保养;推行标准化、规格化的设备保养及管理等手段,以最低成本创造最大附加价值,来达到彻底提高生产效率的目的。
计划保全的推行步骤
计划保全要变为可执行的方式和方法,需要将计划保全具体化和分阶段执行,使管理者有侧重点实施和管理。一般可分为五个阶段或步骤来实施,即设备状态诊断、计划保全的编制和实施、故障解析及改良保养、计划保全的扩大、计划保全值的提升。
(1)设备状态诊断和保养标准建立
只有对每台设备盼现状进行了充分的认识和把握,并根据设备的使用年限、产品特性和质量操作要点等要求,才能制定相应的保养和维护的标准、对应措施和计划,并依据维护标准长效坚持。
①设备现状和保养数据的收集
企业需要采集的保养数据包括:设备的购买时间、价格,验收的情况,平时的保养状况和加工精度情况,故障产生的时间、状况、原因及解决方法。这些数据记录得越详细,对于制定保养计划就越有救果。记录保养数据最好的方法是建立设备档案。设备从进厂开始,直到报废都要入档,档案中除了记录设备的构造原理、设计原理、线路图、操作规程外,还要包括设备的保养记录。其来源主要是:机械设备卡、设备使用和操作说明书、润滑说明、编制的保养和检查标准等。
②保养数据的分析方法
对于设备的保养记录,应进行科学详细的分析,分析数据的规律、机器故障发生的环境、故障原因等,由此制定出合适的保养计划,从而防止故障的发生。通常要进行平均故障时间、保养月报、保养比率这几种数据的统计,如表1所示。
表1 保养数据的分析方法
分析方法 | 含义 | 作用 |
平均放障时间(MTBF) | 设备在一般情况下平均出现一次故障的时间 | 以寿命周期确定点检、保养、零部件库存和使用周期 |
保养月报 | 每个月对设备保养情况的报告 | 分析当月保养情况以提高保养效果 |
保养比率 | 已实施预防设备占工厂设备总量的百分比 | 分析预防保养在保养中的比例 |
(2)计划保养的编制和实施

①保养计划编制
保养计划的准确性决定了保养的有效性,同时也决定了经济性。因此在编制保养计划时,应制定以设备操作者和设备维修人员夯中心的保养计划。
②实施目标管理,确定保养工作的目标
在编制了可行的保养计划后,就应该设定管理目标。策划并鼓励能使全员参与的方案,达到保养时效快、品质好和成本低的目的。
③职能区分、授权负责、落实保养
将总目标层层分解,拟定和落实在保养中对各级人员和各设备、各单位目标的要求。
a.对现场主管的要求
督导所属实施每日保养工作,机器设备小战障的调整,协助保养单位共同执行预防保养。
b.对保养人员的工作要求
协助现场主管调整小故障,切实做好预防保养工作,修理、维护工作尽量安排生产以外的时间,避免影响生产。
c.对保养负责人及主管的要求
全力支持预防保养之各项活动,督导所属及考孩其保养成果,达到人人保养的目的。合理协调、落实沟通,以达到经济有效的保养目的。要有完整充实的保养记录,以供分析、检讨,作为改善的依据。确定预防保养方针。
d.生产单位的职责
每日应检查的工作,短时间不易发现的检查,操作上盼辅助工作,操作时能发觉的异常报告,协助保养人员的支援工作。
④重点(关键)设备的计划保养
重点(关键)设备是整个生产过程中的瓶颈,重点设备如果出现问题,可能会造成整个生产的中断与生产链的切断,因此这类设备是保养中的重点关注和优先实施对象。重点设备的计划保养主要包括重点设备的选定,保养基准的制定,保养方式的选择和保养计划表的制定。
重点(关键)设备的确定可以按照“PQCDS”原则来确定,如表2所示。
表2 “PQCDS”原则
P(Production) | 1.瓶颈设备;2.产量变动较大的设备;3.无备用生产设备;4.与同业比较生产性低的设备;5.故障较多的设备;6.故障影响较大的设备 |
Q(Quality) | 1.影响品质较大的设备;2.品质变动较大的设备;3.因故障而发生品质变化的设备;4.品质要求较高的设备;5.容易疏忽而又会影响品质的设备 |
C(Cost) | 1.使用高价原料的设备;2.需要较多员工的设备;3.耗能源多的设备;4.因故障招致生产损失较大的设备 |
D(Delivery) | 1.很多种类产品通过的设备;2.接近末端工序的设备;3.影响生产时限的设备;4.因局部故障而导致全线停机或迟延的设备 |
S(Safety) | 1.安全设备;2.故障结果影响环境的设备;3.故障结果影响职业卫生的设备 |
⑤保养组织
制定出保养计划表之后,就应该根据计划内容实施,定期召开保养检讨会,确定保养计划。通过保养计划,保证设备的正常运行和生产的正常开展。在保养中对于维修人员的组织可以采用以下几种方式。
a.分区保养,即将各台设备落实到具体的专业保养人员,由指定的人员负责对应的设套备,这种好处是责任明确,考核清晰,工作迅速;保养人员的生产意识较强;生产与保养间协作密切;保养人员对设备状况熟悉,保养工作有效。但是也存在无法机动管理、机动性差,人员间的本位意识强,生产为先,影响保养工作的开展等缺点。
b.集中保养,即设备不指定专门的专业保养人员,这种方式的优点是统一指挥调度,人力物力运用灵活;工作联络、协调容易;器材统一管理,减少库存;技术水准容易提升。但是也存在如果工厂面积大,保养人员无效工作时间增多;对机器操作、熟练度和状态了解较差;生产与保养本位主义较强等缺点。
c.折中保养,即采取集中+分区的保养方式。
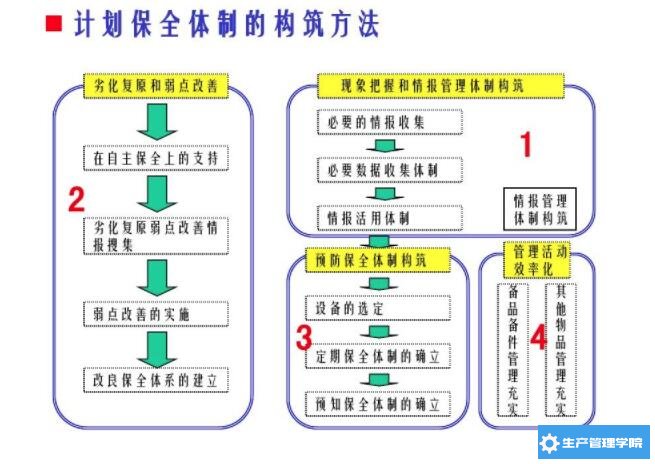
(3)故障的解析和改良保养
①确定设备的薄弱环节
依据点检(操作者和专业人员)、巡检、设备普查、维修和监控等动态资料,寻找薄弱设备和设备薄弱环节,及时组织审理,确定当前应解决的项目,提出改进方案;设备管理部门应组织有关人员对改进方案进行审议,审定后列入检修计划;设备薄弱环节改进实施后,要进行效果考察,作出评价意见,经有关领导审阅后,存入设备档案。凡属下列情况均属设备薄弱环节:运行中经常发生故障停机而反复处理无效的部位;运行中影响产品质量和产量的设备、部位;运行达不到小修周期要求,经常要进行计划外检修的部位(或设备);存在不安全隐患(人身及设备安全),且日常维护和简单修理无法解决的部位或设备。
②故障分析方法
专业保养人员应针对每种设备的原理、设计和构造等,确定不同的分析方法。通过专业人员向普通员工讲解,使员工了解到故障的原因,确定是多发故障、经常发生故障还是重大故障,然后找出排除故障的方法。
③防止事故的再次发生
解决了一次故障之后,怎么防止故障的再次发生,是我们要解决的首要问题。防止故障再次发生主要有五个步骤:分析和复原,分析故障原因,故障接触,制定标准,最后根据标准进行日常的管理。按照这五步就能防止故障的再次发生。
(4)计划保养的扩大
①计划保养的扩大
计划保养不仅要在生产设备上实施,而且应推广到其他方面,如进行保养性提升的研究、保养的效率化的研究、制定生产历程表和保养历程表。这些规章制度的确定可以大大缩短整修的时间。
②备品备件的管理
保养维修设备需要使用大量的备品备件和易损件,在对其进行管理时,应该按照突发性和计划性进行分类管理,其管理状态将直接影响到设备维修结果,进而影响生产的进程。因此,加强对其的有效管理也是一个重要的环节。
③进行改良保养
为了改良保养,机械使用人必须把故障状态详细记录,并积极提出防止故障再发生的改善提案。机械设计人员将保养人员所提出的故障记录及改善提案作为根据、讨论内容,将机械改善为不容易故障,容易保养的机械,成为更有效率的机械。其改良保养方向:性能分析、故障分析、材料研究、设计变更、超载防纸装置、防腐防锈、操作标准建立、其他。
(5)计划保全质的提升