01线平衡的定义
丰田公司的创新之一是将流水线从装配环节拓展到了整个生产过程,如及加工、冲压、焊接等,实现生产整个过程的“一个流”。尽管生产流水线与装配线上的作业任务性质不同,但流水线设计的原理是一致的,线平衡问题的研究内容是一致的动作分析就是通过观察手、足动作和眼、头活动,把动作的顺序和方法与两手、眼的活动联系起来详尽地分析,用记号记录和分类,找出动作顺序和方法存在的问题、单手等待、不合理动作以及浪费动作等问题并加以改善的一种分析方法。应用动作分析可以消除动作浪费进一步提高生产线平衡率和设备利用率。
02线平衡的作用
03线平衡的实施步骤
第二步:建立山积图。将各工序分解后的动作时间以叠加式直方图进行研究。
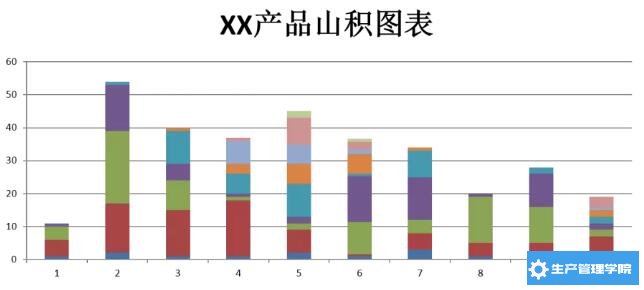
第三步:计算初始数据(改善前线平衡率、人时产能等)
第四步:利用ECRS(取消、合并、重排、简化)原则进行优化。常见的线平衡改善方式有以下几种。
1.研究瓶颈岗位作业,利用动作改善优化作业工时,或使用低成本工装、工具提升作业效率。
2.将瓶颈岗位部分作业转移至空闲岗位操作。
3.增加人力分担瓶颈岗位工作。
4.将空闲岗位作为分解给其余不饱和的岗位,实现减员增效。
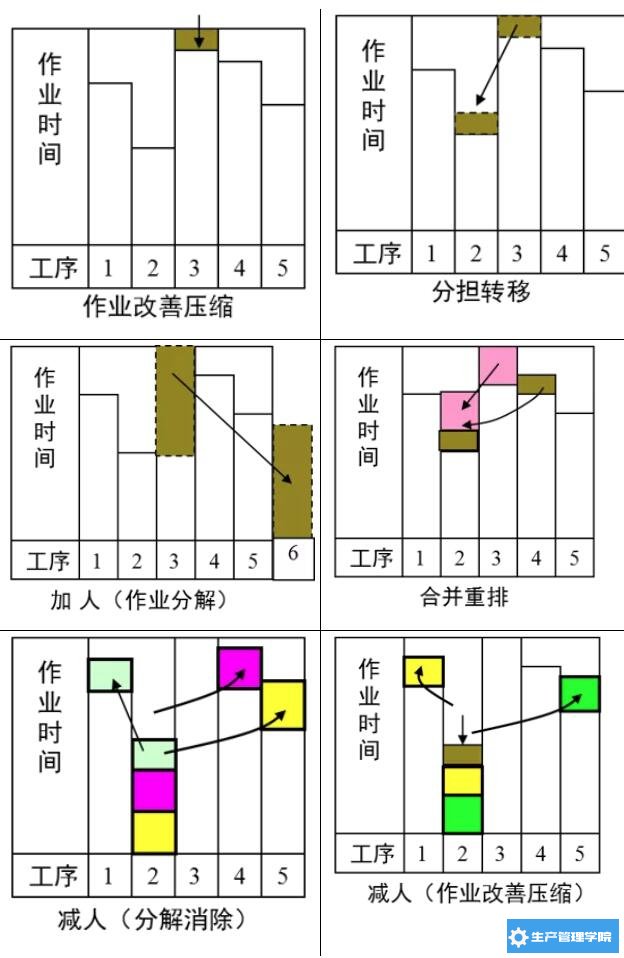
第六步:更新作业指导书,实施作业标准化。
如何改造线平衡的五步法
线平衡是如何影响效率的?以下两个生产线同样做轮滑鞋,请问谁的效率高?
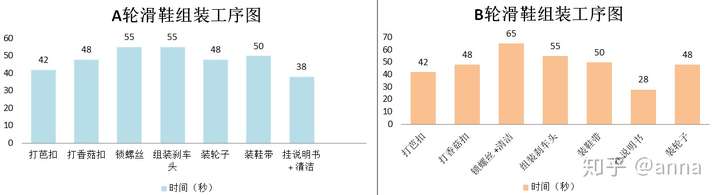
而A和B最大的差异就是瓶颈工位的不同,造成线平衡率的不同。敲黑板划重点: 瓶颈工位的产出决定了一条生产线的最大产出。对于劳动密集型的产业(如服装,鞋业等),人力无可厚非是工厂最重要的资产和驱动。在提高人均效率,降低人工制成成本中,线平衡成了当仁不让很多老板们追求的目标,因为线平衡越高,在现有人数的基础上产出就越高,OEE越高,成本也就越低。
有了省钱的动力,我们一起来看看怎样实施线平衡吧:
- 测量做完一个完整产品需要的时间(SOT : Standard operating time)。 建议找一个相对熟练的操作工,测量他/她从头到尾完成一个产品的组装需要的时间。用熟练工的时间作为标准,排除了因为不熟练造成的很多没有价值的等待时间,让目标更加具有挑战性。要知道,一个不熟练工人所花时间有时候可能是熟练工的3倍。如轮滑鞋的例子中,350S即为SOT.
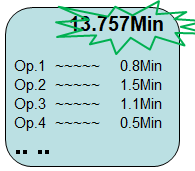
CT: 指两个工位之间所花的时间。
CT = SOT/ Manpower (分配的人数)
日产量 = 工作时间/ SOT *分配的人数
当有产出压力时,优先考虑产量。如下图蓝色区域所示,SOT = 13.757 分, 假设每天有效工作时间是569分钟,则每天每人的产出是:569/13.757=41.36个,要求每天产出550个,则需要人数为:550/41.36=14人。对应的CT为:13.757/14=0.983 分。 同理可推当优先考虑先有人数和机台限制时候的CT.
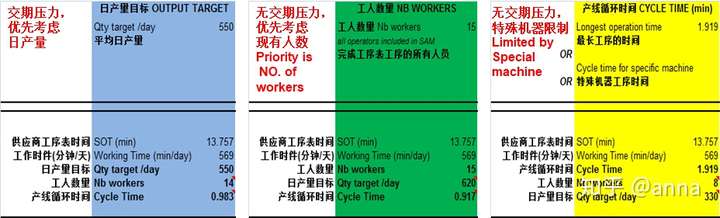
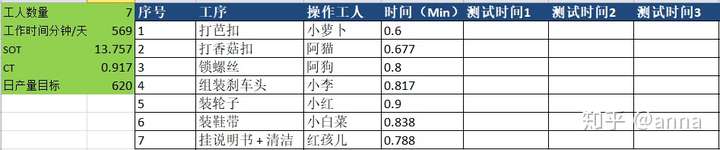
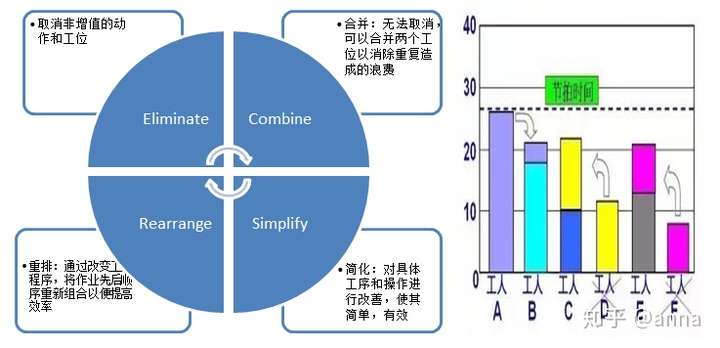
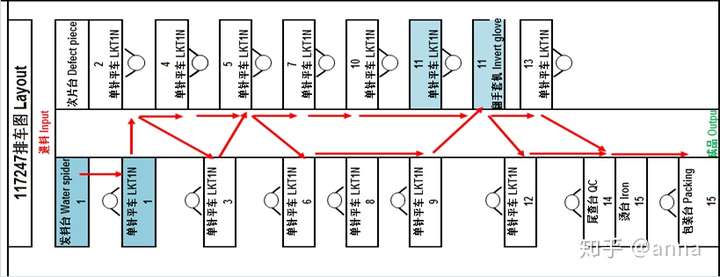
线平衡率= 各工序纯工时总和/人数*循环时间。以下的线平衡率是:5.42/(0.9*7)= 86%.
一般来说,平衡损失率在5%-15%以内是可以接受的,否则就需要进行改善。
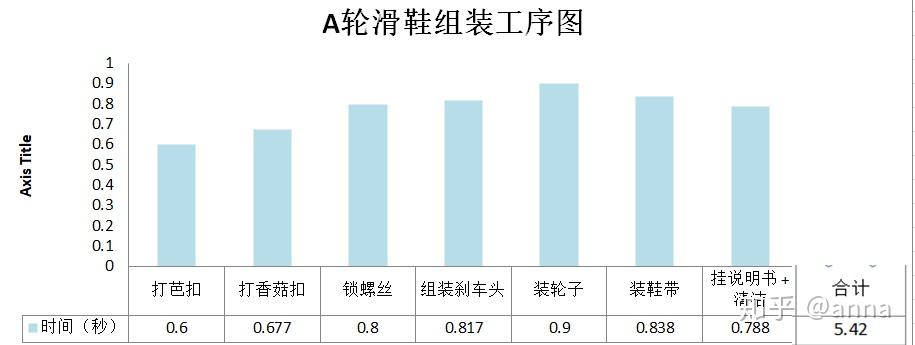
以上介绍了如何改造线平衡的五步法。线平衡只是工具,要想提高效率,降低成本,比工具更重要的是管理,是体系,建议各位从线平衡开始,由点到面,首先定义出最优线平衡的标准,然后建立起可视化管理进行记录,然后定期线gamba发现问题,逐步营造出PDCA持续改善的精益文化,只有这样才能实现可持续的企业升级,实现高绩效低成本的经营目标!